Eine Bandsäge ist ein interessantes und recht vielseitiges Werkzeug. Bisher hatte ich nicht die Mittel auf einem Haufen, um eine passende kaufen zu können. Dann der Tag im Jahr 2017, an welchem ich zum ersten Mal auf YouTube die Bandsäge Videos von Matthias Wandel sah. Gespannt habe ich mir alle Bauvideos angesehen und für mich entschieden: „Das kannst Du auch!“ Kurz darauf hatte ich die Pläne für die 16“ Bandsäge gekauft und heruntergeladen. Von da an hing in der Werkstatt am Schornstein-Zentralmassiv der 1:1 Ausdruck des Rahmens.
Soweit, so gut! Nun musste ich mir Bretter besorgen um den Rahmen zu bauen. Eigentlich wollte ich dafür Palettenholz zusammen laminieren, hatte aber keine Paletten greifbar. Die Alternative, Paletten im Baumarkt zu kaufen war doof und teurer als gehobelte Leimholzbretter zu erwerben (was langweilig gewesen wäre). Ein weiteres Problem war das nicht Vorhandensein einer Abrichte/Dickenhobel aber…
eins nach dem Anderen: Weihnachtsgeld gibt es ja meist im November und das kam mir sehr zu Pass. Bei eBay gab es eine Abricht-/Dickenkombination für knapp 250€. Taugt nicht viel dachte ich, ist aber finanziell erreichbar (Ich hatte damit leider Recht :-). Das Teil gekauft und geliefert bekommen und beim ersten Test gleich an der Abricht Dickenverstellung den Handgriff abgebrochen – na toll.
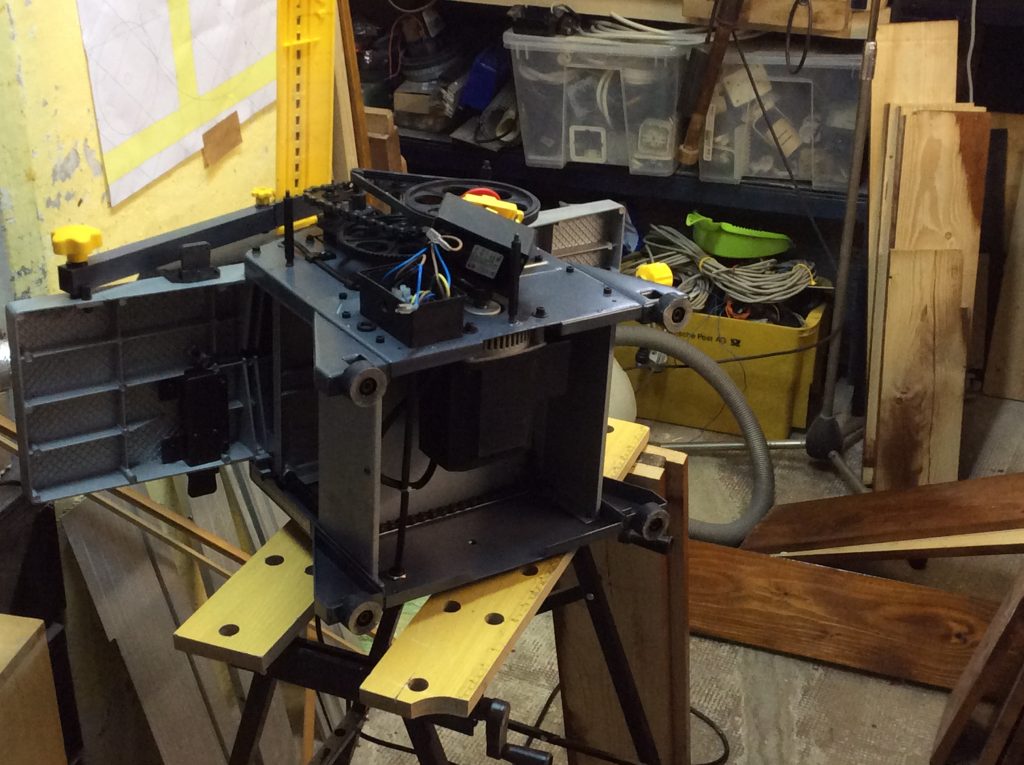
Zwei, drei Wochen zuvor hatte ich Bretter mit einer Dicke von etwa 21 mm auf dem Sperrmüll um die Ecke gefunden und nach Hause geholt. Das traf sich gut, da das Holz durch eine vermutlich feuchte Lagerung in einem Keller sogar teilweise richtig nass war, brauchte es Trocknungszeit. Als dann der Dickenhobel fertig einsatzbereit war, war das Holz auch soweit getrocknet, dass es gehobelt werden konnte. Das Hobeln war eine laute und dreckige Angelegenheit die einen ganzen Vormittag dauerte und mindestens eine thermische Pause verlangte. Da ich nicht genau wusste, wie die Thermosicherung funktionierte, habe ich erst mal einiges zerlegt und dabei gelernt, wie die Sicherung funktioniert – 15 Min warten und dann erst geht der Spaß zurück zu stellen…
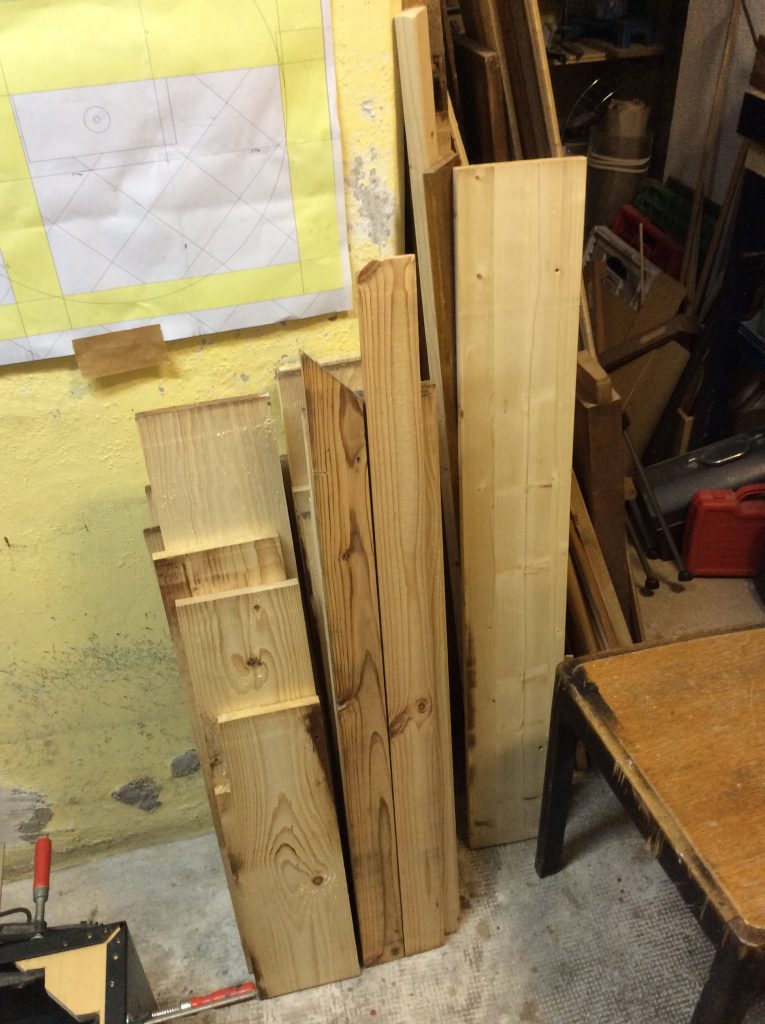
Nun hatte ich also zwar fertig geformte aber nicht schöne Bretter und hätte theoretisch beginnen können. Herr Dr. Truppe von Lets Bastel war inzwischen auch der Meinung eine Bandsäge bauen zu wollen. Ein Wettlauf? Wohl kaum. Ich hatte mir zur Bedingung gemacht, alle notwendigen (Holz)Teile von Hand mit Fuchsschwanz, japanischer Ryoba oder Laubsäge auszusägen. Das war echt eine Challenge – 2 1/2 Tage habe ich abends Holz kaputt gesägt und war immer wieder erstaunt, dass die Bretter fast so aussahen wie sie sollten. Da ich mir bezüglich Schleifen, Bohren und Fräsen keine Zwänge auferlegt hatte, konnte ich mir wenigstens die Oberflächenbearbeitung etwas erleichtern. Nach ca. 12 Wochen Abends und an Wochenenden bauen, war ich endlich soweit fertig, dass ich mich auch als stolzer Bandsäge Besitzer bezeichnen konnte.
Im folgenden gehe ich etwas auf Probleme und Stolpersteine die mir begegnet sind, ein.
Stolpersteine
Bretter Hobeln
Zunächst schien es einfach, die ergatterten Bretter abzuhobeln und in brauchbares Baumaterial zu verwandeln. Es sollte aber etwas schwieriger werden als gedacht. Das erste Problem, war die recht preisgünstig erworbene Abricht- /Dickenhobelkombination mit dem „Stahlmann Logo“ darauf. Es musste vieles daran erst gangbar gemacht werden und der Einstellknopf für die Spanstärken Verstellung brach bei der ersten Abrichthöheneinstellung einfach ab. Ein Bastler kennt da aber keinen Schmerz – einfach ein Stück M 8er Gewinde angeschweißt und den Knopf daran festgeschraubt. Dann (nach viel Einfetten) konnte endlich die Spandicke eingestellt werden und ich konnte mit Hobeln losgehen. Viel Späne konnte ich nicht abtragen, da der Krach und das unsaubere Hobelbild eigentlich unerträglich waren. Also habe ich weniger dicke Späne abgenommen und dafür länger gebraucht, hatte dann aber leidliche Qualität die natürlich am Anfang und Ende der Bretter durch die Einzugswalzenungenauigkeit in der Stärke schwankten.
Rahmenteile zuschneiden
Das Zuschneiden der vielen Rahmenteile von Hand war dann doch eine nicht zu unterschätzende Herausforderung. 2 1/2 Tage habe ich gesägt, dann lagen alle nötigen Teile bereit.
Da ich nicht so viel Material hatte wie nötig war, musste ich Restbretter nochmals verleimen und weiter verwenden – man könnte sagen es ist eine Recycling Säge 🙂
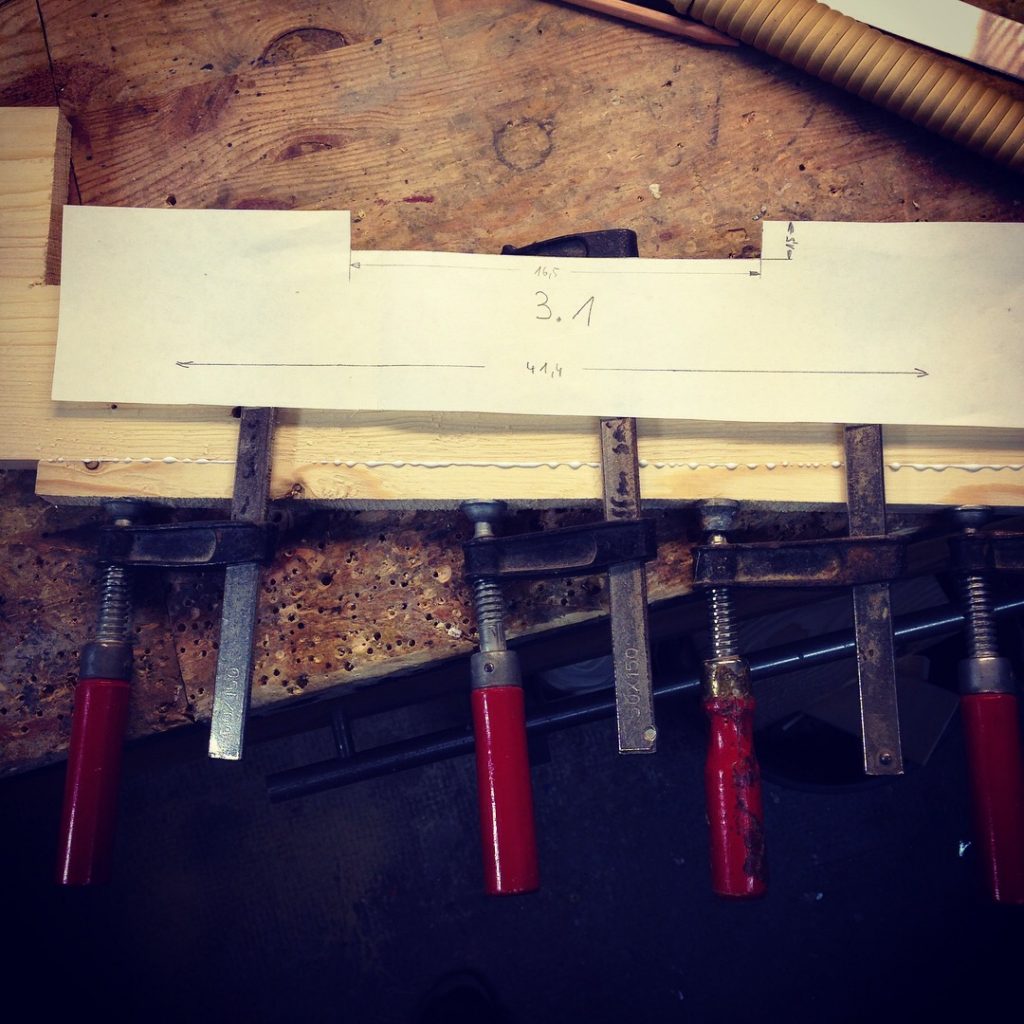
Glücklicherweise hatte ich mir von allen herzustellenden Teilen, Papierschablonen gefertigt die ich zum Anreißen und zum späteren Identifizieren verwendet habe. Trotzdem habe ich einige Teile falsch zugeschnitten – „Abgeschnitten, abgeschnitten, immer noch zu kurz!“. War nicht wirklich tragisch – da die laminierte Konstruktion viele Fehler verzeiht – aber auch nicht wirklich schön!
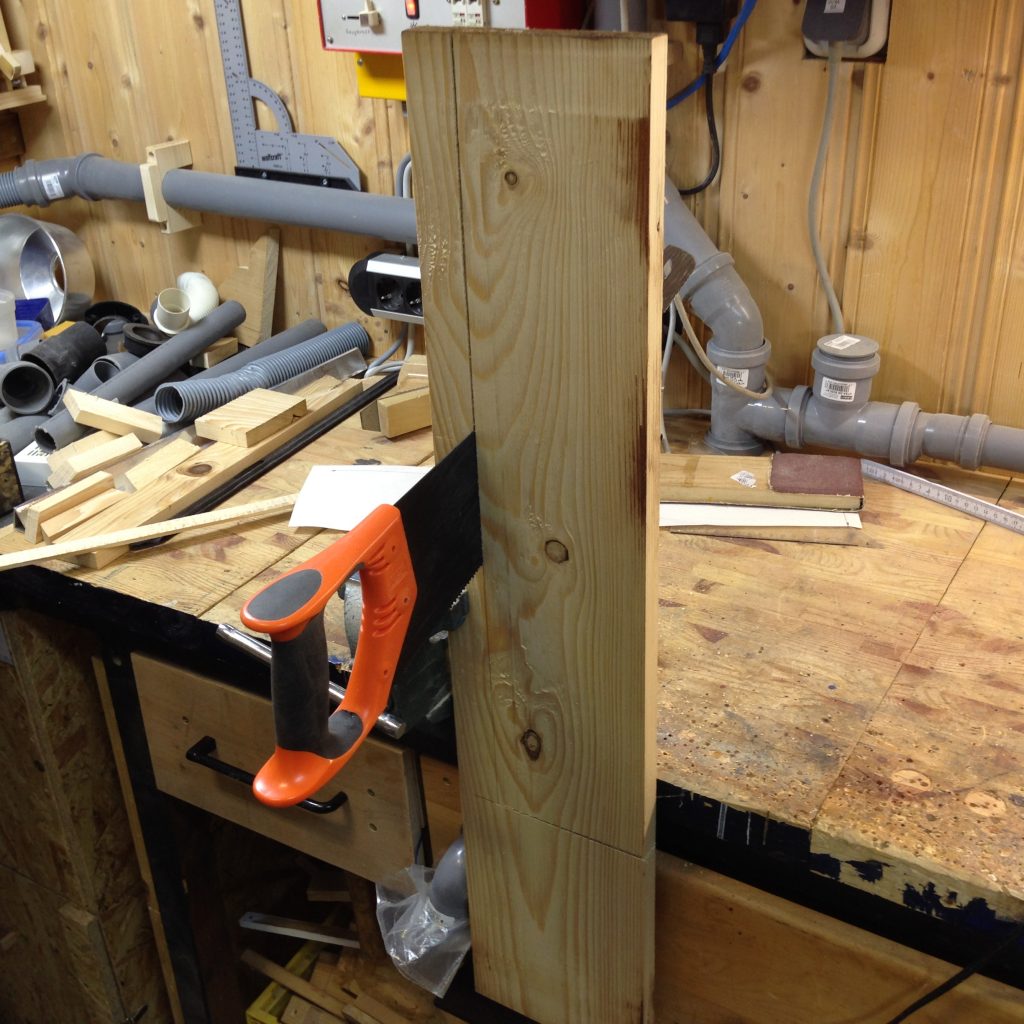
Danach hatte ich dann mehrere Teilestapel herum liegen, auf die ich jeweils die Schablone gelegt hatte. Ganz zu Anfang hatte ich mir die Laminier-Zeichnung ausgedruckt, farbig markiert und mit Nummern versehen. Diese Nummern hatte ich auch auf die Schablonen und einzelnen Teile geschrieben, was den Zusammenbau des Rahmens sehr erleichterte.

Der von Matthias Wandel stammende Rat, den gesamten Stapel einmal aufeinander zu legen und dann die einzelnen Lagen für sich zusammen abzulegen ist möglichst zu beachten – und das rät Einer, der es nicht beachtet hat…Ich habe daraus gelernt!
Rahmen zusammen leimen
Den Rahmen zu verleimen hat wieder andere Herausforderungen bereitgehalten. Zunächst wird laut Anleitung und Video, die erste Lage winklig zusammen geleimt. Das ist ziemlich einfach und geht recht zügig. Zu beachten ist dabei allerdings ein planer Bauuntergrund der für eine formstabile, rechtwinklige Ausrichtung der ersten Lange wichtig ist. Wird dies nicht beachtet, kann sich der fertige Rahmen so verzogen haben, dass die Laufräder nicht in Flucht zu bringen sind worunter dann die Genauigkeit und Laufruhe des Sägebandes leidet.
Nachdem die erste Lage getrocknet ist, muss diese erste Lage umgedreht werden und alle weiteren Lagen kommen dann sozusagen „hinten“ dran.
Das hatte ich dann wohl übersehen oder nicht daran gedacht…
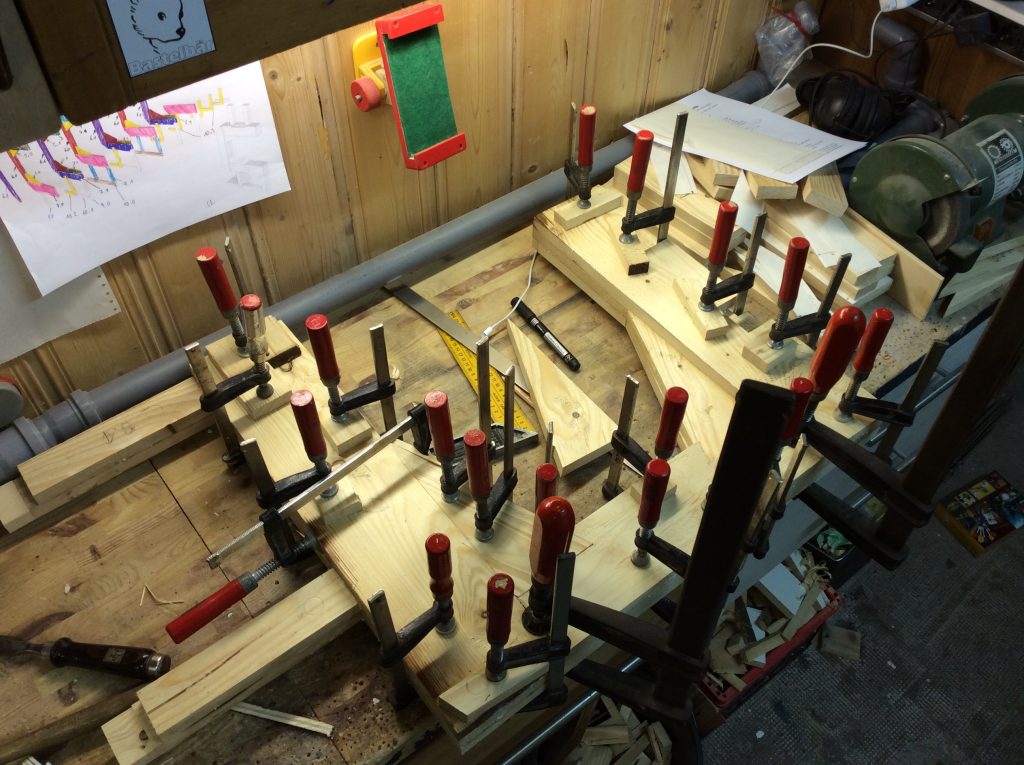
Beim Aufleimen der dritten Lage kam mir das Aussehen des Rahmens dann etwas komisch vor – gerade noch rechtzeitig fiel mir auf, dass die Lagen irgendwie nicht passen wollten. Na ja, was sollte jetzt passieren? Ich habe das Paket einfach umgedreht und nach Anleitung weiter verleimt. Schlussendlich hatte ich dann schon einen passenden Rahmen, wenn auch nicht unbedingt so zusammen gesetzt, wie die Pläne es vorgesehen hatten. Wie schon erwähnt, der Schichtaufbau des Rahmens verzeiht relativ viele Fehler, da er zum Schluss eine Art Block bildet den man auch noch nacharbeiten kann.
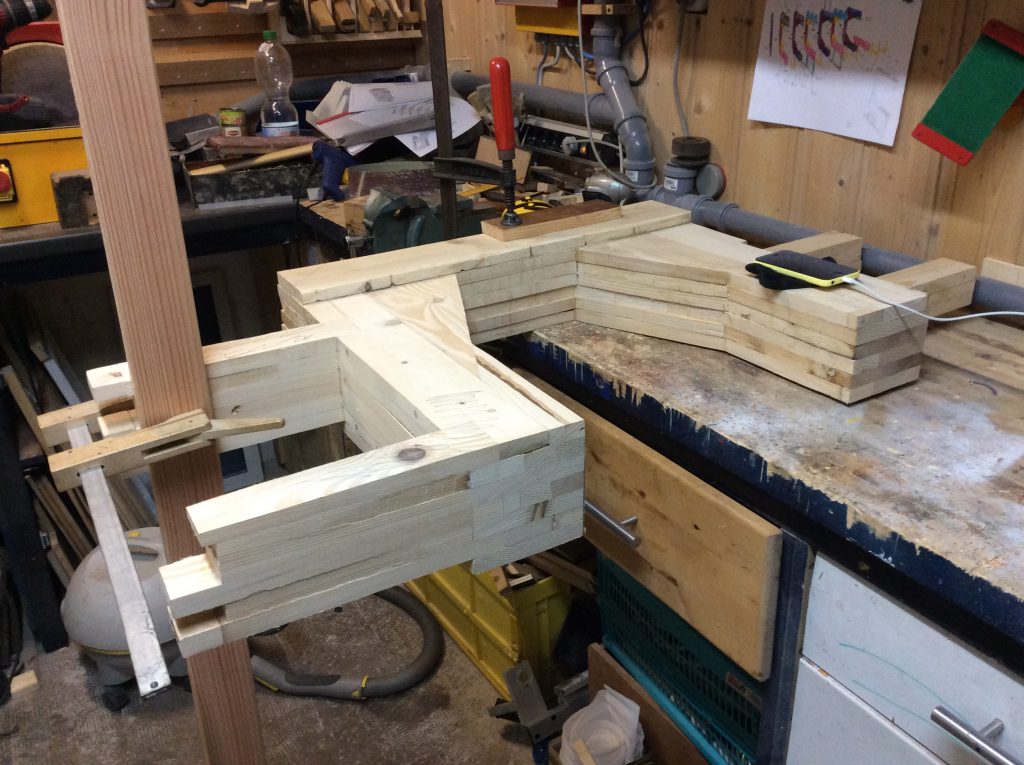
Im vorangehenden Bild deutet sich schon ein weiteres Problem an. Dadurch dass die Werkbank nicht groß genug war, hatte sich der Rahmen etwas verzogen, was an dem dunklen Spalt zwischen Rahmen und Werkbank zu sehen ist. Aber selbst das ließ sich mit Tricks ausgleichen…
Räder bauen und justieren
Weiter im Text:
Die Räder mit einem Durchmesser von 16 Zoll (400 mm) wollte ich nach der Vorlage von Marius Hornberger aus doppelt verleimten 16 mm MDF Material bauen. Also, Baumarkt besuchen und 4 Platten 420 mm x 420 mm zuschneiden lassen. Dieses Maß war mehr als ausreichend für den Zuschnitt der Radkreise. Nun kam das Zusammenleimen von jeweils zwei MDF-Platten, wofür ich wie viele andere „Radbauer“ auch, fast alle meine Schraubzwingen im Einsatz hatte! Nach dem Verleimen und gut Trocknen lassen, wählte ich meine Oberfräse um die Radscheiben auszuschneiden/fräsen. Zu diesem Zweck, musste ich mir aber zunächst einen Fräszirkel anfertigen. Damit war es dann ziemlich einfach, die Kreise auszufräsen obwohl der von mir verwendete Fräser leider zu kurz war. Trotz beidseitigem Zirkel Fräsen, blieb in der Mitte der Scheiben noch genug für eine Stichsägebehandlung stehen. Nach dem Ausfräsen und -sägen der einzelnen Teile,
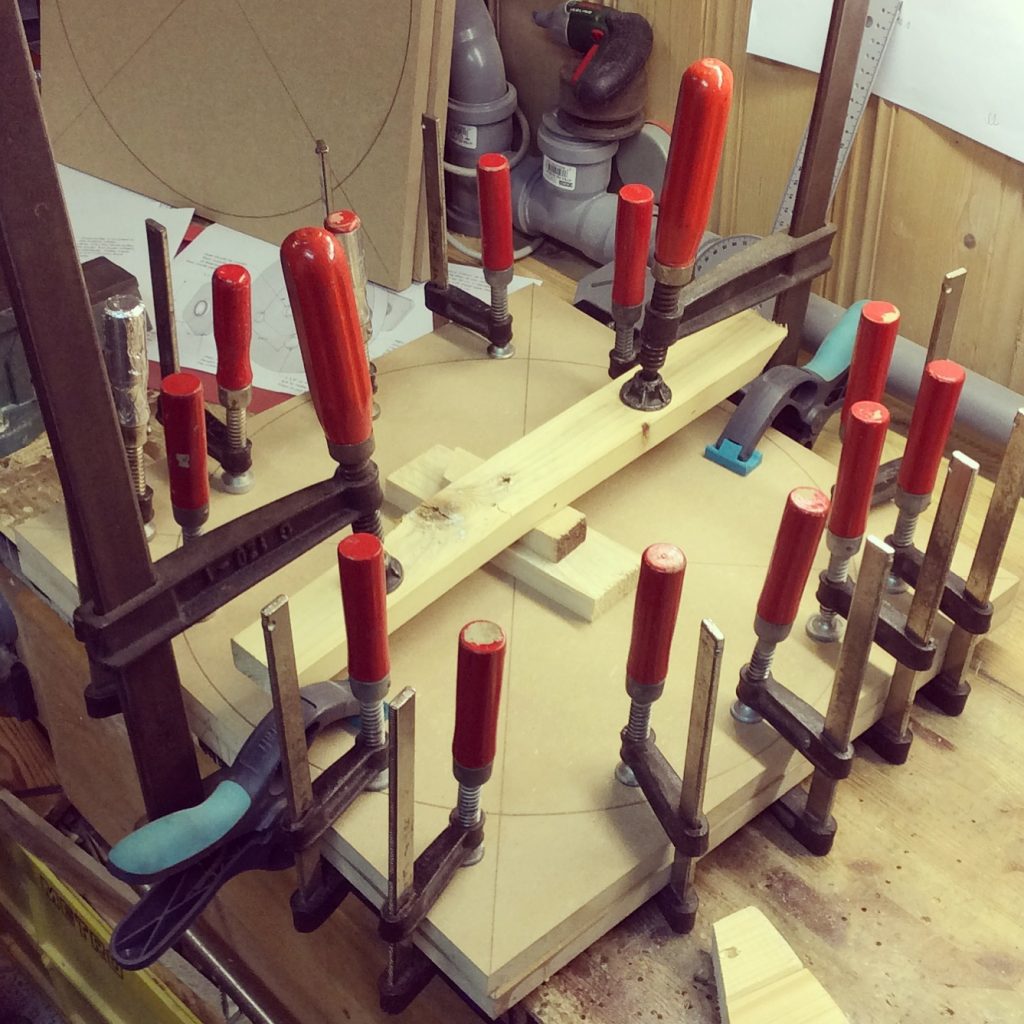
mussten als nächstes die Spann und Gewichtungslöcher mit meinen neuen Forstnerbohrern – die kleineren mit 42 mm und die Größeren mit 50 mm gebohrt werden. Das ging, dank MDF, sehr einfach, zügig und sauber. Anschließend konnte ich dann mit meinem SROL Billigkreisschneider von Amazon, die Kreise für die Presspassung der Lauflager aus den speziellen Lagerscheiben ausschneiden und die Lager einpressen. Diese „Lagerscheiben“ wurden dann mit Hilfe eines Zentrierstücks genau auf einer Seite der Radscheiben ausgerichtet und angeklebt. Die jeweils andere Seite wurde dann in einem etwas aufwendigeren Verfahren auf 0,6 mm Seitenschlag ausgerichtet und dann auch aufgeleimt.
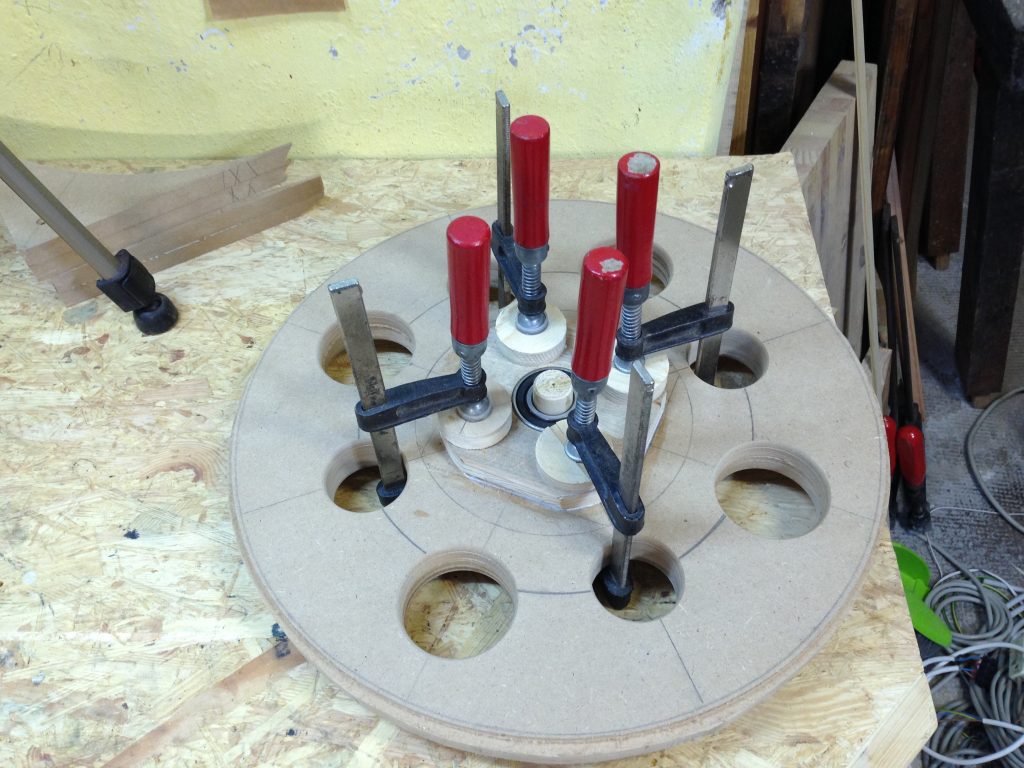
Damit die Räder ohne Umlauf-Schlag laufen konnten, musste ich sie noch abdrechseln. Ohne Drechseleisen ist das aber ein echt mühsames Brot. Dank des weichen MDF-Materials reichten hier zwei, drei unterschiedliche Stechbeitel, die ich vorher gut geschärft hatte. Ich war froh und zufrieden, als ich die Bandlaufkrone zu meiner Erleichterung gleichmäßig fertig gedrechselt und geschliffen hatte. Auch hier war die Lauftoleranz ziemlich gut.
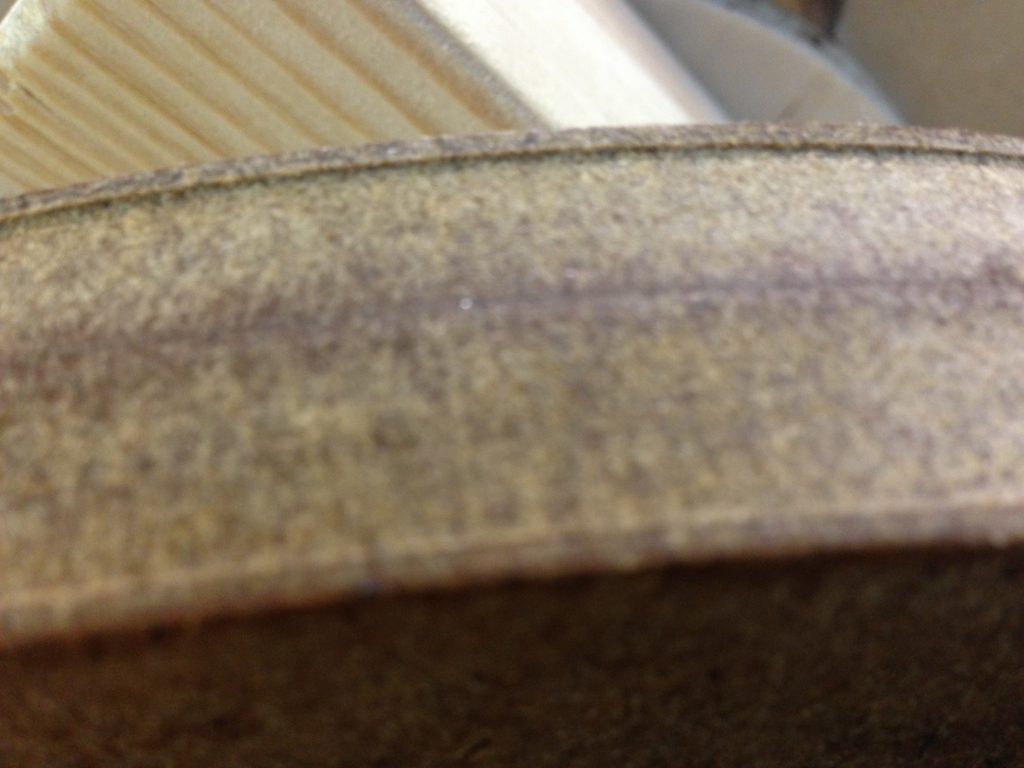
Um zu vermeiden, dass die Zähne des Sägebandes durch den Druck auf die Lauffläche des Rades verbogen werden und sie dadurch ihre Schränkung verlieren, wurde ein frisch gekaufter 12 Zoll Fahrradschlauch zerschnitten, ein der Breite zwischen den Kronenflanken entsprechender Streifen sauber herausgetrennt (nein, nicht mit Ventil) und dann später dort aufgezogen. Damit liegt das Sägeband auf dem Gummi auf und dieser gibt beim Spannen des Sägebandes den Zähnen nach.
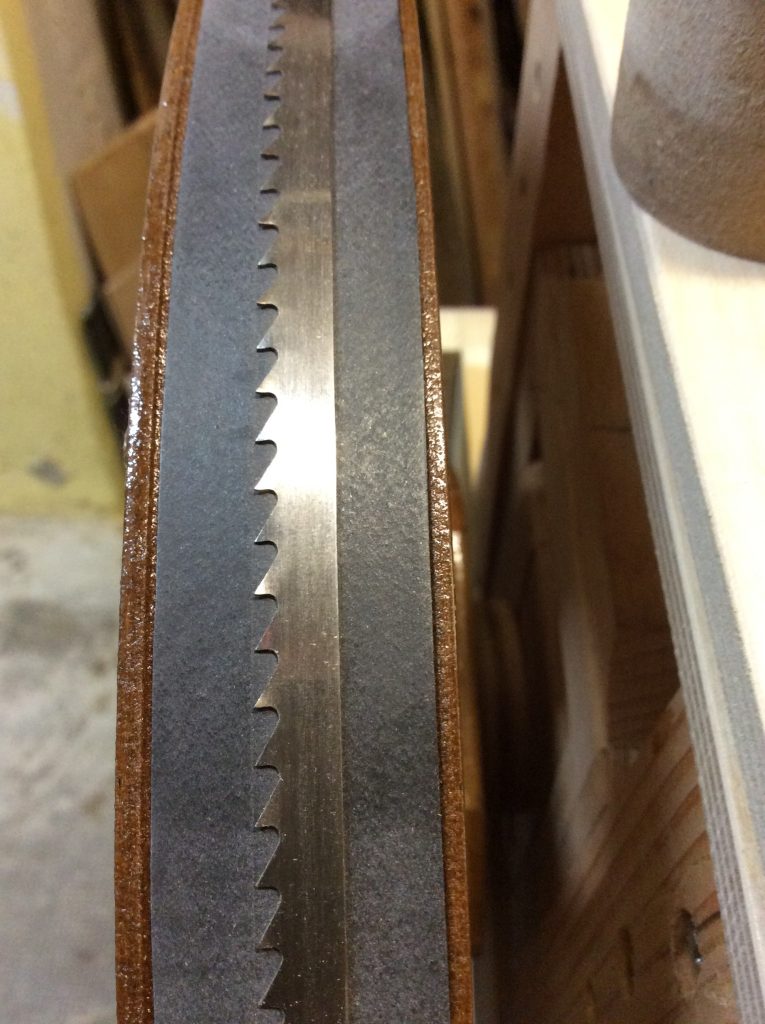
Mit Bootslack wurden nun die fertigen Räder 2 x Oberflächen behandelt. Das gab ihnen gerade auf der Krone eine enorme Festigkeit und gleichzeitig einen guten Look und Schutz.
Da am unteren Laufrad noch die Antriebs Riemenscheibe angebracht werden musste – man möch’t ja auch einen Antrieb haben – musste ich diese erst fertigen. Auch diese Scheibe habe ich, um einen gleichmäßigen Durchmesser zu erhalten, mit dem Fräszirkel aus 15 mm Multiplex gefräst. Dann musste ich aus der Riemenscheibe, die Außenmaße der Lagerscheibe mit meiner Stichsäge ausschneiden, damit sie am Laufrad auch angebracht werden konnte. Um die V-Nut für den Riemen in die Scheibe zu bekommen, habe ich mir eine kleine Vorrichtung gebaut und einen alten Fräser im entsprechenden Winkel angeschliffen und geschärft. Nun war es ein Leichtes, die Nut einzufräsen (siehe Bild unten)…
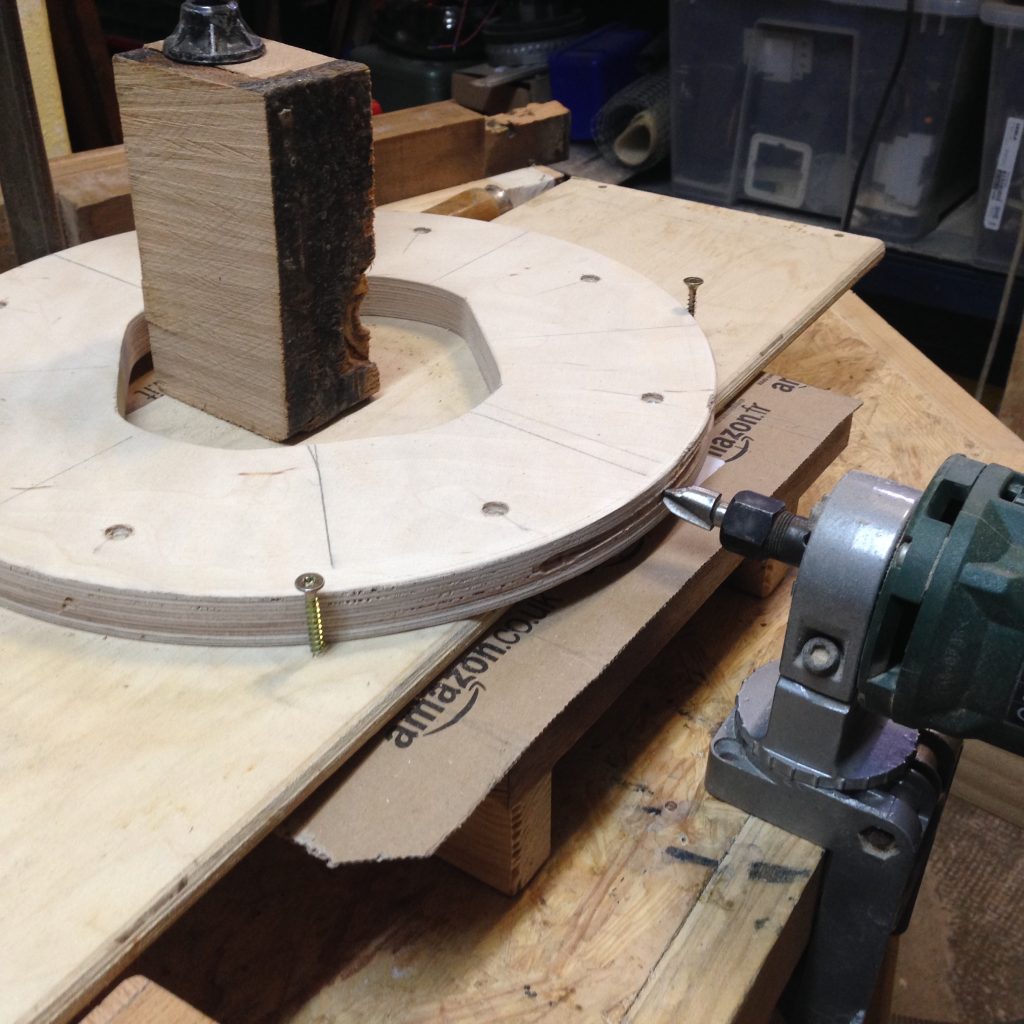
Bandführungen und andere Hartholzteile bearbeiten
Aus Hartholz – in meinem Fall war es Buche – wurden die Bandführungen, die obere Bandführungshalterung, die Achsaufnahmen und die gesamte untere Bandführung gebaut. Die obere Bandführungshalterung war recht einfach herzustellen. Ein Buchenstück auf Maß bringen, eine Ausklinkung am unteren Ende und eine 45° Fase an einer Längskante anbringen und fertig. Andere Teile waren da schon etwas schwerer und mussten erste aus mehreren Teilen zusammen geleimt werden. Am Ende war es Fleißarbeit, viel Sägen und Feilen und immer wieder messen und vergleichen ob die Teile mit den Vorgaben übereinstimmten.
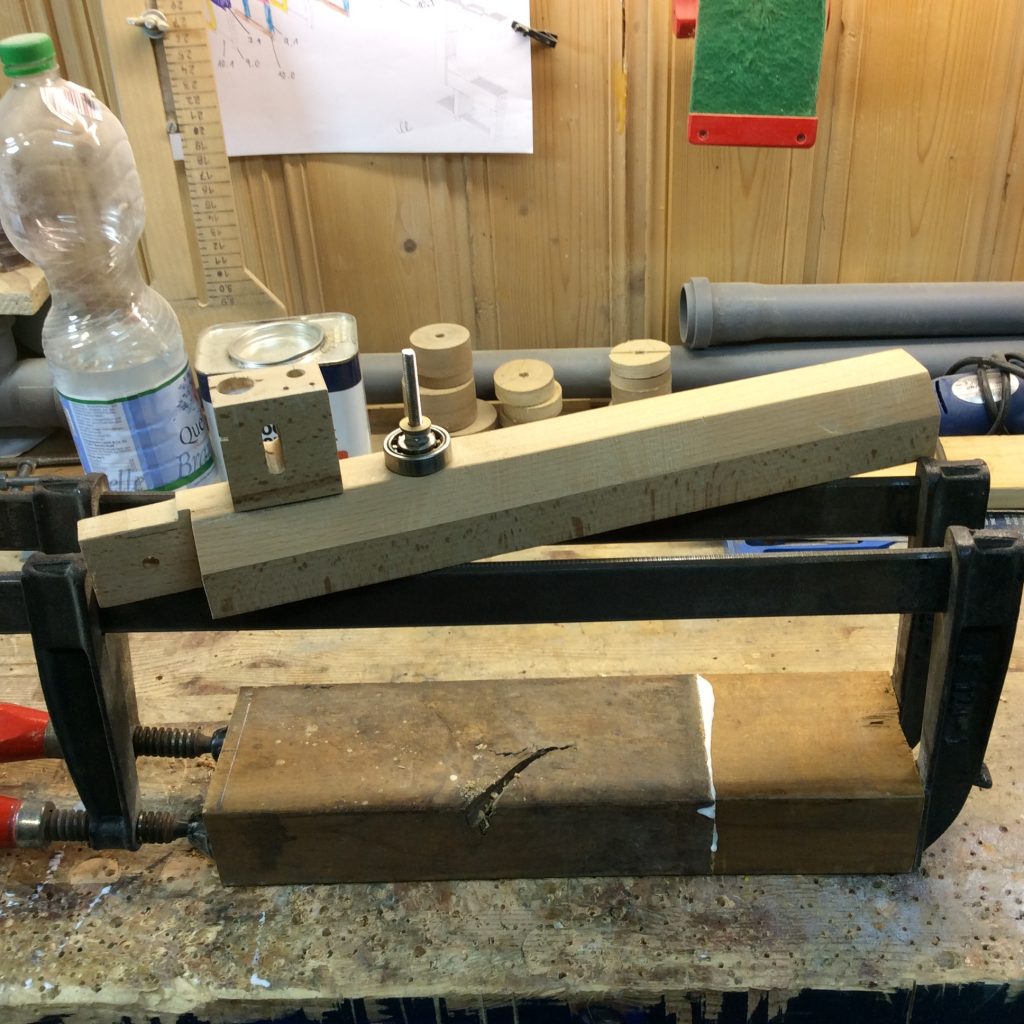
Radlagerungen
Um das Sägeband aufziehen zu können, war es natürlich zunächst notwendig, die Randhalterungen herzustellen und zu montieren. Die obere war da im Vergleich zur unteren ein wenig komplizierter, da diese aus einem verschiebbaren Rahmen und der Einstell- und Spannvorrichtung für das Sägeband besteht. Diesen Rahmen leimte ich wieder aus Buchenholzteilen zusammen und verstärkte die Ecken mit eingeleimten Holzlamellen. Das ergab eine gute mechanische Stabilität und erhöhte die Kraft, die der Rahmen vom Sägeband aufzunehmen in der Lage ist. Dann musste die eigentliche Achsaufnahme aus mehreren Teilen zusammen geleimt und zurecht gesägt bzw. geschliffen werden.
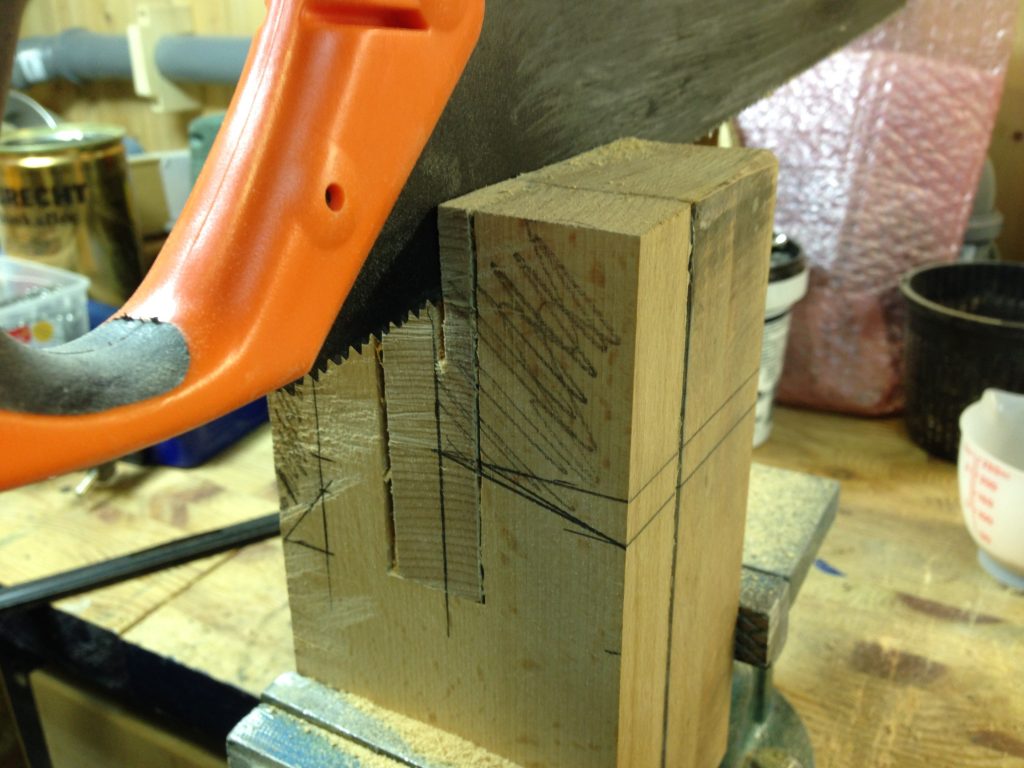
Um die Achsaufnahme gegen den verschiebbaren Rahmen verstellen zu können, wurde sie an einer unten im Rahmen angebrachten Falz angeschraubt. Oben erhielt sie eine Einstellschraube, die quer zum Rahmen gegen eine Metallplatte am Rahmen drückt und dafür sorgt, das die Achsaufnahme zur Seite geneigt werden kann, um den Laufbereich des Sägebandes auf dem Rad justieren zu können. In den oberen Querholm des verschiebbaren Rahmens wurde eine senkrechte Bohrung für eine 10 er Gewindestange eingelassen, die ich anschließend mit 2K-Epoxid-Kleber eingeklebt habe.
Die Gewindestange wurde nach oben durch zwei Holzfedern und eine oben angebrachte Kurbel in die Lage versetzt, den ganzen Rahmen in den oben am Hauptrahmen angebrachten Führungsholmen nach oben und unten zu bewegen. Diese Einrichtung dient dem Spannen des Sägebandes und ist essentieller Bestandteil der Lagerung. Die untere Wellenhalterung habe ich aus dem für die 16″ Bandsäge vorgesehenen Lagerblock aus Hartholz und der bei der 20″ Bandsäge angebrachten hinteren Halterung zusammengesetzt.
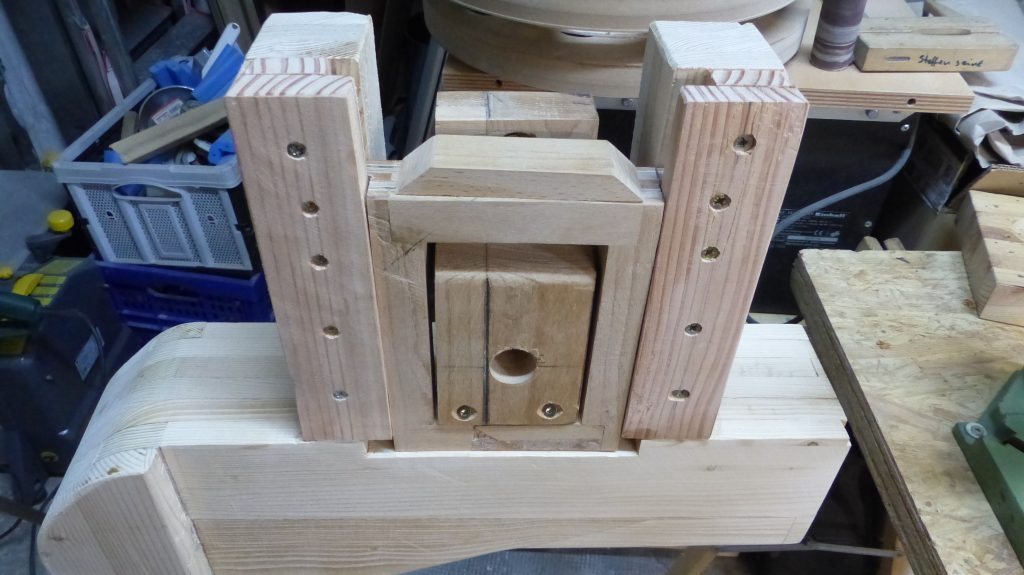
Die 20 mm Bohrung für die Welle zu bohren war ohne vernünftige Ständerbohrmaschine nicht ohne weiteres möglich, weswegen ich die ursprüngliche Bohrung mit einem eingeklebten Rundstab wieder verschießen und nochmals bohren musste. Das hat einiges an Zeit verbraucht und war zum Schluss doch nicht so genau wie ich es hatte haben wollen. Natürlich merkte ich nach der ersten Montage der Räder, dass diese nicht korrekt in der Flucht lagen. Das hat mich nicht so sehr verwundert, konnte ich doch einige der erforderlichen Arbeitstechniken nicht wie gewünscht anwenden. Durch unterlegen von Holz und Pappstreifen unter den Lagerblock der unteren Radaufhängung, brachte ich dieses Rad in Parallelität zum Hauptrahmen (dieser Block hat ja ansonsten keine Einstellfunktion) und hatte dann „nur noch“ die obere Radaufhängung auszurichten. Die obere Halterung war leicht quer zum Hauptrahmen verdreht, was ich nur durch Anpassung der Nuten in den oberen Führungsholmen korrigieren konnte. Nach diesen ganzen (erfolgreichen) Korrekturen, konnte ich mich den Bandführungen und wieder dem Hauptrahmen widmen.
Bearbeitung des Hauptrahmens
Um die obere Bandführungshalterung mit dem Rahmen verbinden zu können war es notwendig, am aufgespannten Sägeband mit einem genauen rechten Winkel am Rahmen die Lage des Bandes zu markieren. Nun musste der Betrag, um den das Band in der Bandführung versetzt war, abgerechnet werden um letztendlichen zum Maß des Führungsfalzes zu kommen. Dieser wurde sauber angezeichnet und mit dem Fuchsschwanz auf die geforderte Tiefe ausgesägt. Dann erfolgte die Nacharbeit mit Hobel und Stechbeitel (und Schleifleinen), um die geforderte Ausrichtung (rechter Winkel zur Bandführungshalterung) zu erhalten. Das war ein wenig schwierig, weil ich zu diesem Zeitpunkt keine perfekt geschliffenen Stechbeitel mehr hatte. Da als Befestigung für die obere Bandführungshalterung von Matthias Wandel eine Klemmung vorgesehen war, musste diese natürlich erst angefertigt werden. Die Klemmung besteht aus einer in die Stirnseite des Hauptrahmens geklebten 10mm Gewindestange, einer Sterngriffschraube und dem Klemmkörper selber. Dieser Klemmkörper besteht aus einer kleinen 15 mm starken Multiplexplatte, an die an einem Rand eine Hartholz Dreiecksleiste und gegenüber eine Multiplex Führungsleiste geleimt wurde. Außerdem wurde genau in der Mitte ein 10,5 mm Loch gebohrt. Für die weitere Freigabe von Sägehöhe, wurde ca. 20 mm darunter ein Weiteres Loch mit dem gleichen Durchmesser gebohrt.
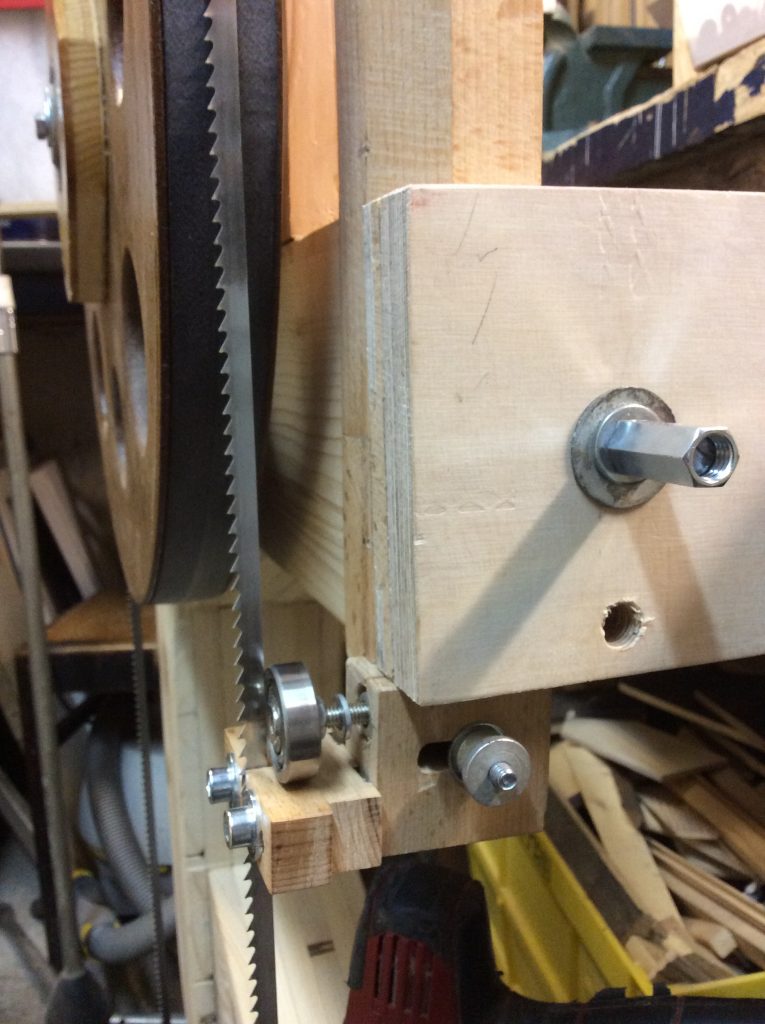
Damit war die obere Bandführungshalterung fertig gestellt und es fehlte noch die Bandführung selber. Diese wurde mit Säge, Bohrer und Forstnerbohrer aus vier Hartholzstückchen gefertigt. Nach der Komplettierung durch mehrere Schrauben sowie ein Kugellager, kam die Sägetischhalterung mit dem Querholm für die Trunions und die Bandführung daran.
Der Sägetisch und die Trunions
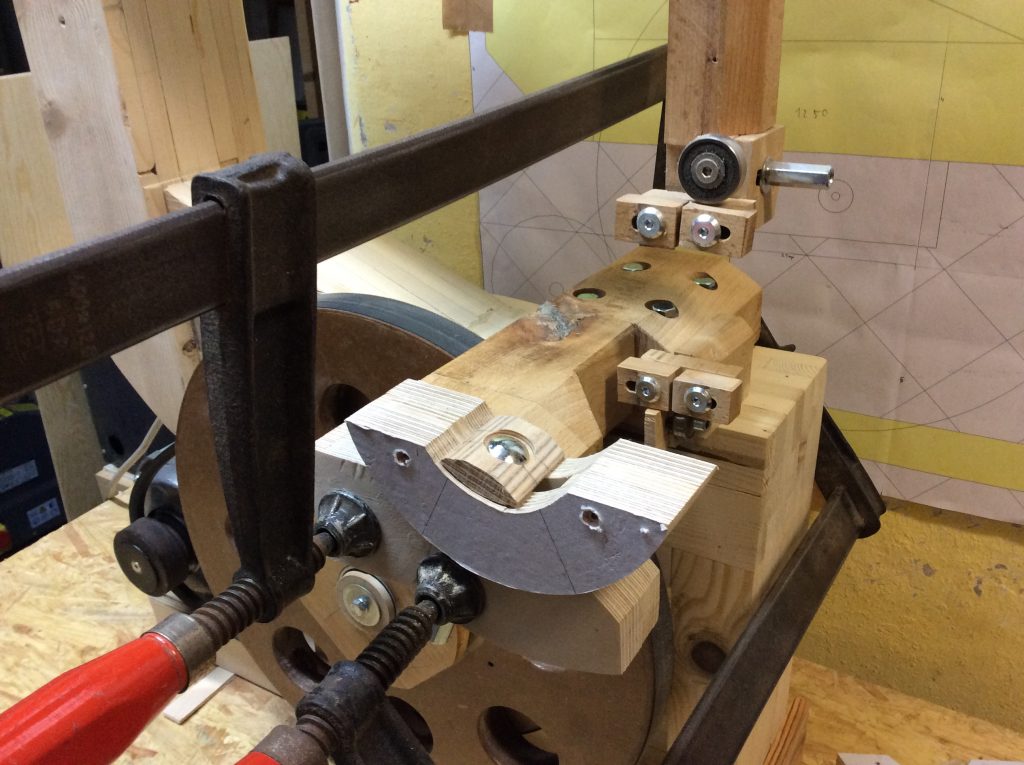
Die Sägetischhalterung, bestehend aus dem Querträger, den Trunions und dem Unter- und Obertisch war nicht so schwer zu bauen, wie ich ursprünglich angenommen hatte. Nachdem ich die erforderlichen Teile ausgesägt und fertig bearbeitet hatte (was aufgrund der erforderlichen Genauigkeit einiges an Zeit verschlungen hat) konnte ich einfach alles zusammen Leimen und -Bauen. Ha!…von wegen einfach zusammen bauen. Als ich die Trunions an den Querträger angeleimt hatte merkte ich, dass ich die Breite des Querträgers etwas übertrieben hatte (so meinte ich zumindest) Also habe ich die rechte, hintere Trunion wieder abgesägt und die Querträgerbreite angepasst) Nach erneutem Verleimen hatte ich dann eine Unterkonstruktion, auf die ich zuerst den unteren und dann den oberen Sägetisch befestigen konnte. Das Ausrichten der Tische war, ausgehend von den gewünschten Winkelstellungen zu Sägeblatt ein bisschen Schwierig, wurde aber trotzdem gut geschafft. Dann wollte ich die Sterngriffe für die Trunions ausmessen und ausschneiden. Dabei merkte ich das irgendwas nicht so stimmt wollte wie es sollte. Der von mir wieder abgesägte und wieder angebaute Trunion auf der rechten Seite bot jetzt nicht mehr genug Platz für eine Sternschraube. Hmm, da hatte ich es wohl zu gut gemeint. Egal, ich habe mir durch Vierkantgriffe beholfen die wesentlich schmaler waren, für die ich aber aus 6 mm Multiplex einen speziellen Maulschlüssel mit der Bandsäge fertigen musste.
Um den Sägetisch nicht immer extra auf 0 ° einstellen zu müssen, brachte ich hinten am Querträger zwei Höhenanschläge an, die eine schnelle und genügend genaue Ausrichtung in der Horizontale ermöglicht.
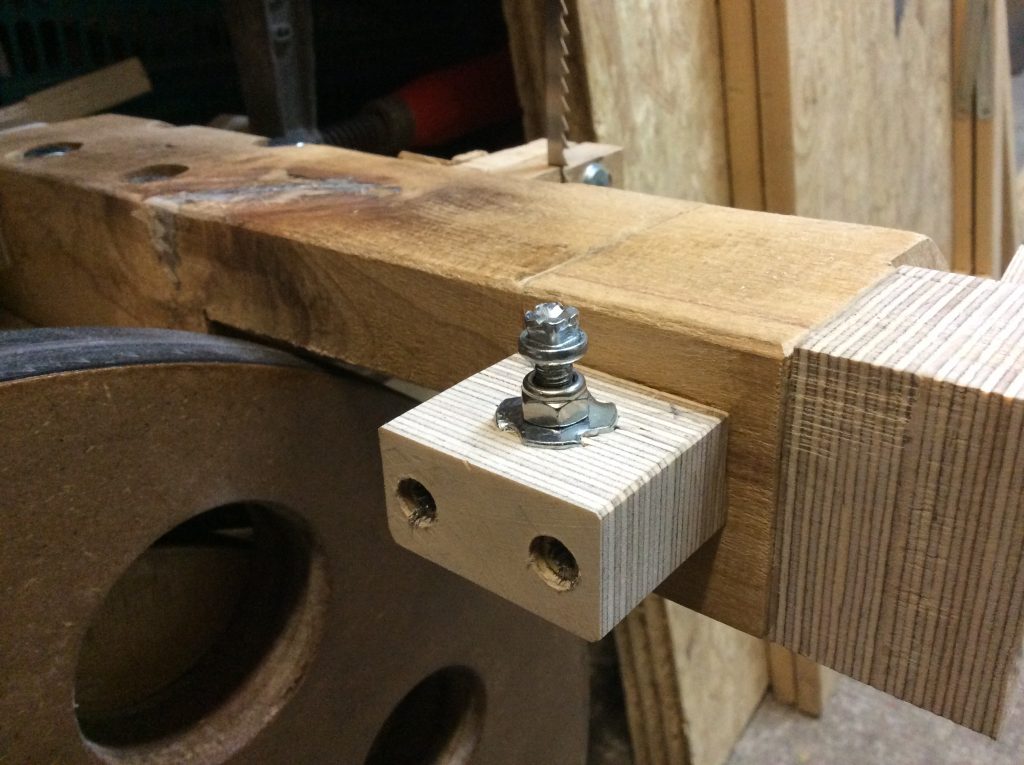
Den Sägetisch musste ich aus zwei Teilen zusammen Dübeln und Leimen. Das hatte den Vorteil, dass ich eine vorhandene 22 mm Siebdruckplatte verwenden konnte, aber auch den Nachteil, dass ich keine zusammenhängend wirkende Oberfläche hatte. Um meine Version eines Parallelanschlages verwenden zu können, montierte ich an der Vorderen Stirnkante ein 8 mm T-Nut Aluprofil. Darunter bekam die Platte zunächst eine Verstärkung aus Douglasienholz die der Stabilisierung und Erhöhung der Dicke dienen sollte. Diese wurde dann später durch einen umlaufenden Rahmen aus Buchenholz ersetzt.
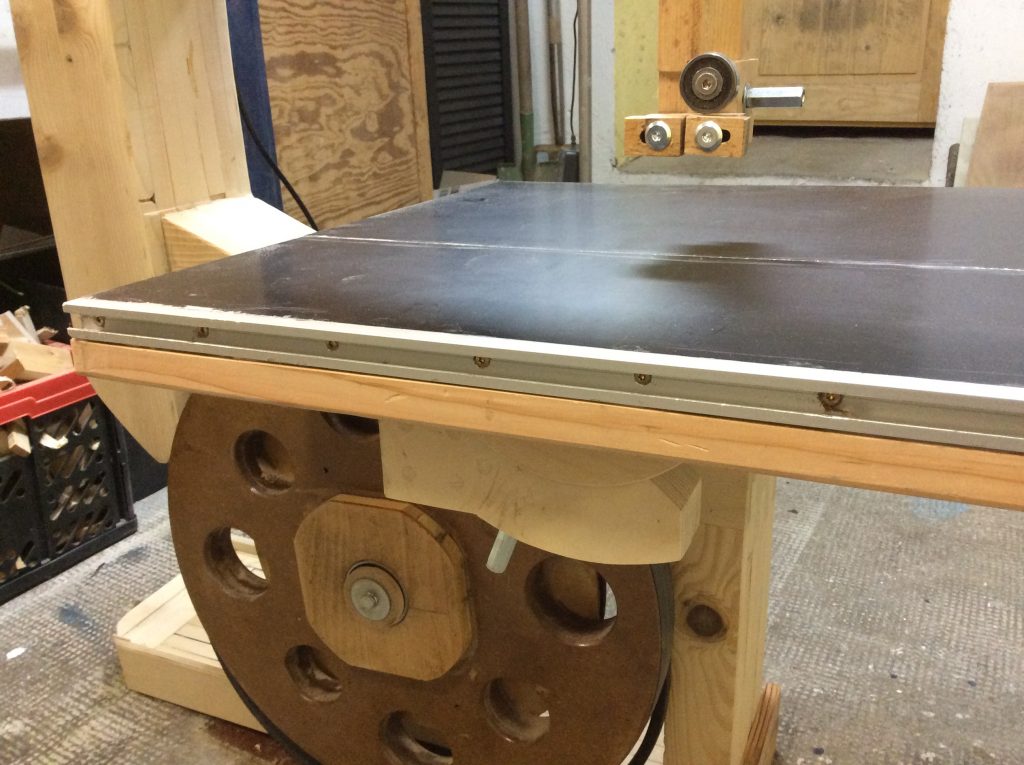
Die erste Version, hatte auch noch eine weitere Fehlerstelle. Es fehlte die parallel zum Sägeblatt verlaufende T-Nut Schiene für die Führung der Kreisschneidevorrichtung und natürlich fehlte die gesamte Sägebanddurchführung mit Einlegeplatte für 90° und 45° Schnitte. Die zweite Version hatte dann alle genannten Merkmale und zusätzlich noch eine aufgeklebte Stahlblechplatte als Tischoberseite. Ihr meint: „Schade um die Siebdruckplatte. Da hätte Palettenholz gereicht!“ – Stimmt, aber die Idee mit der Stahlplatte war nicht von Anfang an vorhanden. So kann’s manchmal gehen.
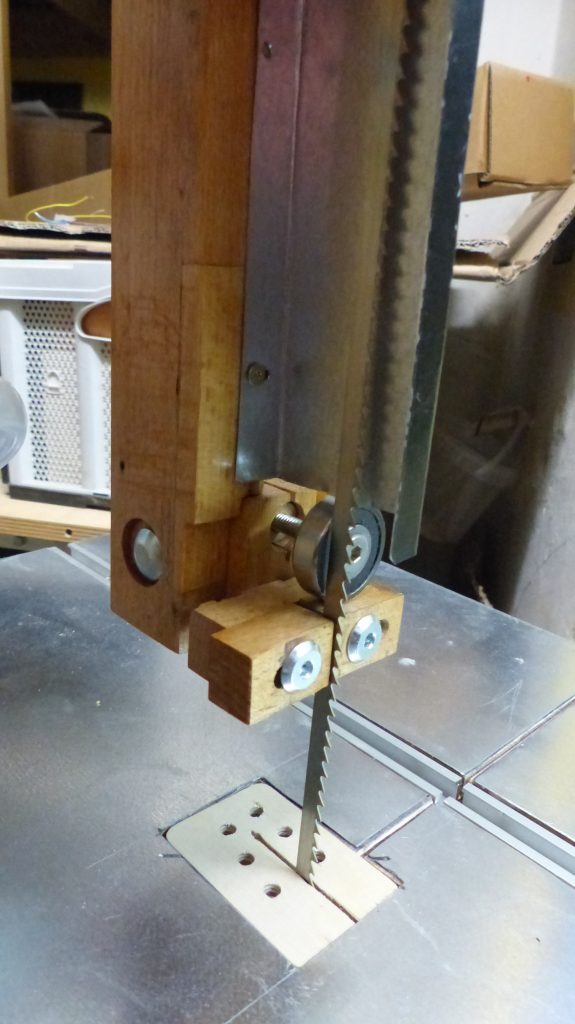
Motorhalterung
Der vorläufige Zusammenbau war dann relativ schnell erledigt, es mussten aber noch andere (Klein) Teile hergestellt werden. Dabei kam der Motorhalterung eine besondere Bedeutung zu, da der Motor ja korrekt und sicher eingebaut werden, aber auch noch justierbar sein sollte.
Dazu habe ich zunächst die Auflagefläche am hinteren unteren Rahmen begradigt und geschliffen und mit einer Führung für eine Gleitplatte aus Multiplex versehen. Auf diese wurde dann mit selbst gebauten Stehbolzen der Elektromotor befestigt.
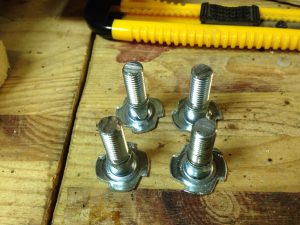
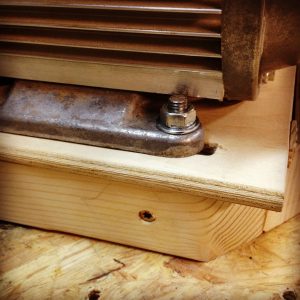
Nun war die Bandsäge fast betriebsbereit… aber nur fast. Es fehlte noch alles was eine sichere Handhabung und Bedienung möglich macht – Die Abdeckungen und Sicherheitsvorrichtungen…
Sägeunterkonstruktion
Um die Säge nicht jedes mal auf den Tisch hoch und runter wuchten zu müssen, habe ich dann erst mal eine Konstruktions- und Baupause eingelegt und zunächst die fahrbare Unterkonstruktion der Säge gebaut. Von einem lieben Instagram Kollegen (Vielen Dank an Bruno -blackforest59) hatte ich einen Satz Schwerlastrollen geschenkt bekommen, die für dieses Teilprojekt wie geschaffen waren. So nahm ich die erforderlichen Maße ab und konstruierte aus Kanthölzern einen stabilen Rahmen, in den ich dann Plattenreste als Wandelemente eingebaut habe. Schwerlastrollen drunter geschraubt, Hellgrau lasiert und überlackiert und Bandsäge darauf befestigt. Nun konnte ich endlich die Säge hin und herfahren und musste die mittlerweile schon recht schwere Maschine nicht mehr per Muskelkraft herum wuchten. Das war eine enorme Erleichterung.
PS.: Allerdings habe ich es bis Stand heute noch nicht geschafft, die noch fehlenden Schubladen in den Sägeständer einzubauen. Diese werden aber noch nachgeliefert…
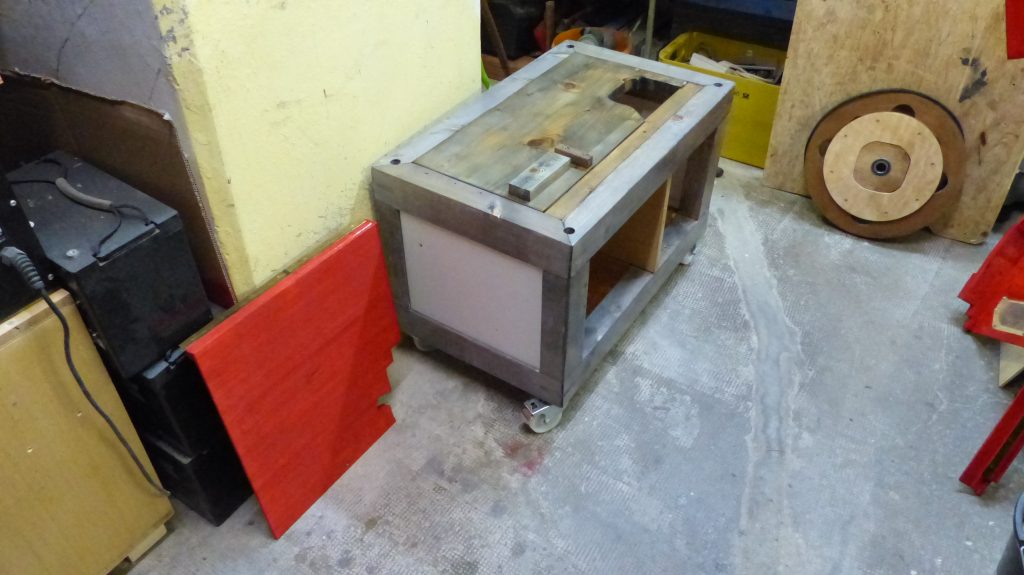
Sicherheitsabdeckungen
für die obere Radabdeckung hatte ich mir etwas besonderes ausgedacht. ich wollte nicht die von allen nachgebaute eckige Bauform haben, sondern die früher bei vielen Bandsägen eingesetzte runde Bauform nachbilden. Das war bezüglich der Stabilität natürlich schon ein Herausforderung. Matthias Wandel hat die Rahmenteile der Abdeckungen mit Lamellen verbunden um zusätzliche Stabilität zu erreichen. Da ich alles händisch sägen wollte (außer den Stichsägeaktionen) musste ich mir da was anderes ausdenken. Also leimte ich kleine, winklig zurecht geschliffene Holzstückchen auf der hinteren Montageplatte der Abdeckung zu einem Bogen zusammen und fräste und Schliff sie nach dem Trocknen auf eine halbwegs gleichmäßige Dicke ab. Um nun die Lamellen zu ersetzen, leimte ich auf der Vorderseite dieses Bogens einen gebogen ausgesägten Streifen Sperrholz auf, der die Stabilisierung übernehmen sollte. Da diese Schichtung ähnlich wie der Aufbau einer Dreischichtplatte funktioniert, ist die Stabilität auch wirklich gegeben. Die untere Radabdeckung habe ich von der 20″ Bandsäge übernommen und angepasst. Zur unteren Radabdeckung gehört natürlich auch die Abdeckung der Hinterwand (unter der Achsaufhängung), die Treibriemenabdeckung, und die Leiste am vorderen Ende der Bandsäge. Dort habe ich mir von verschiedenen Herstellern das gängige Prinzip der Absaugschlauchanbringung abgeschaut und durch ein Blastgate ergänzt. Nun ist es möglich, die Bandsäge mit einer aktiven Absaugung zu betreiben oder die Späne einfach passiv in den darunter angebrachten Spänefang fallen zu lassen. Das ist günstig, wenn man spät Abends noch sägen will ohne die Absaugung 🙂
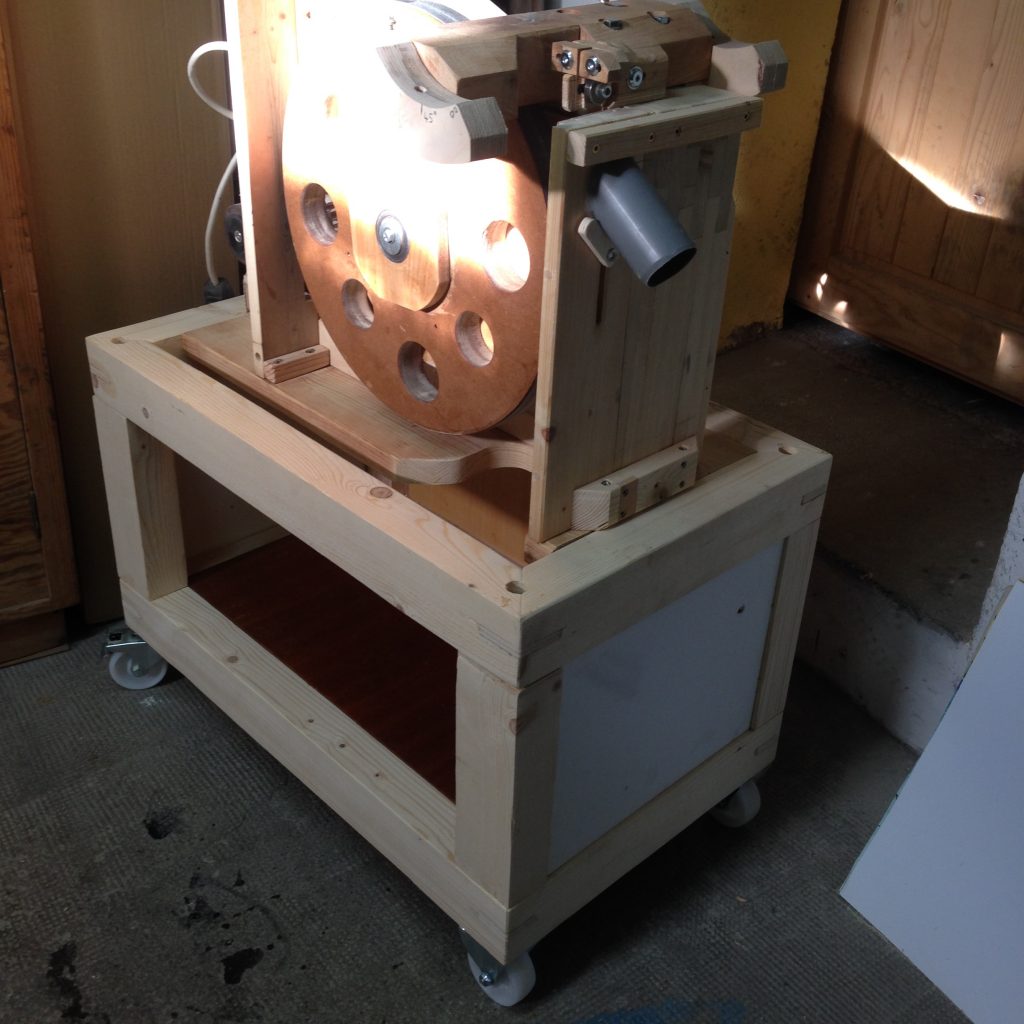
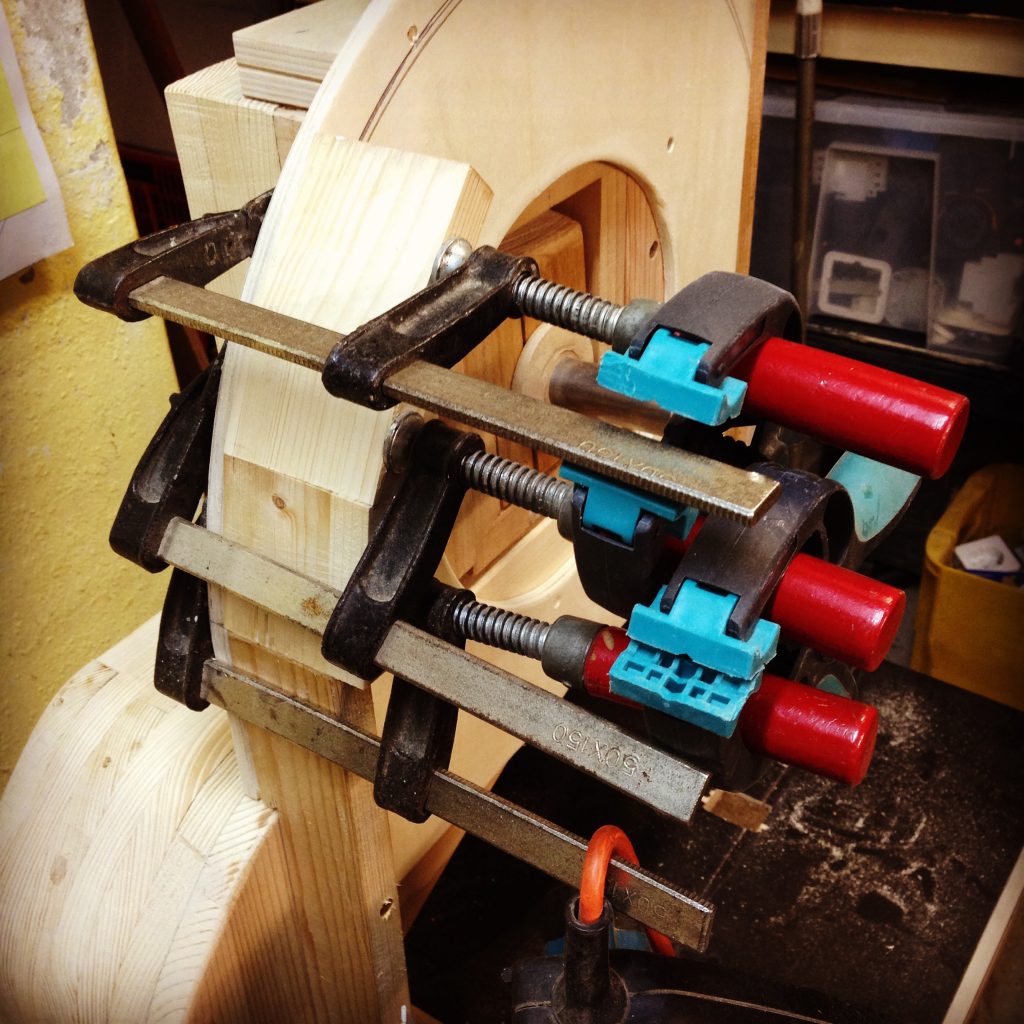
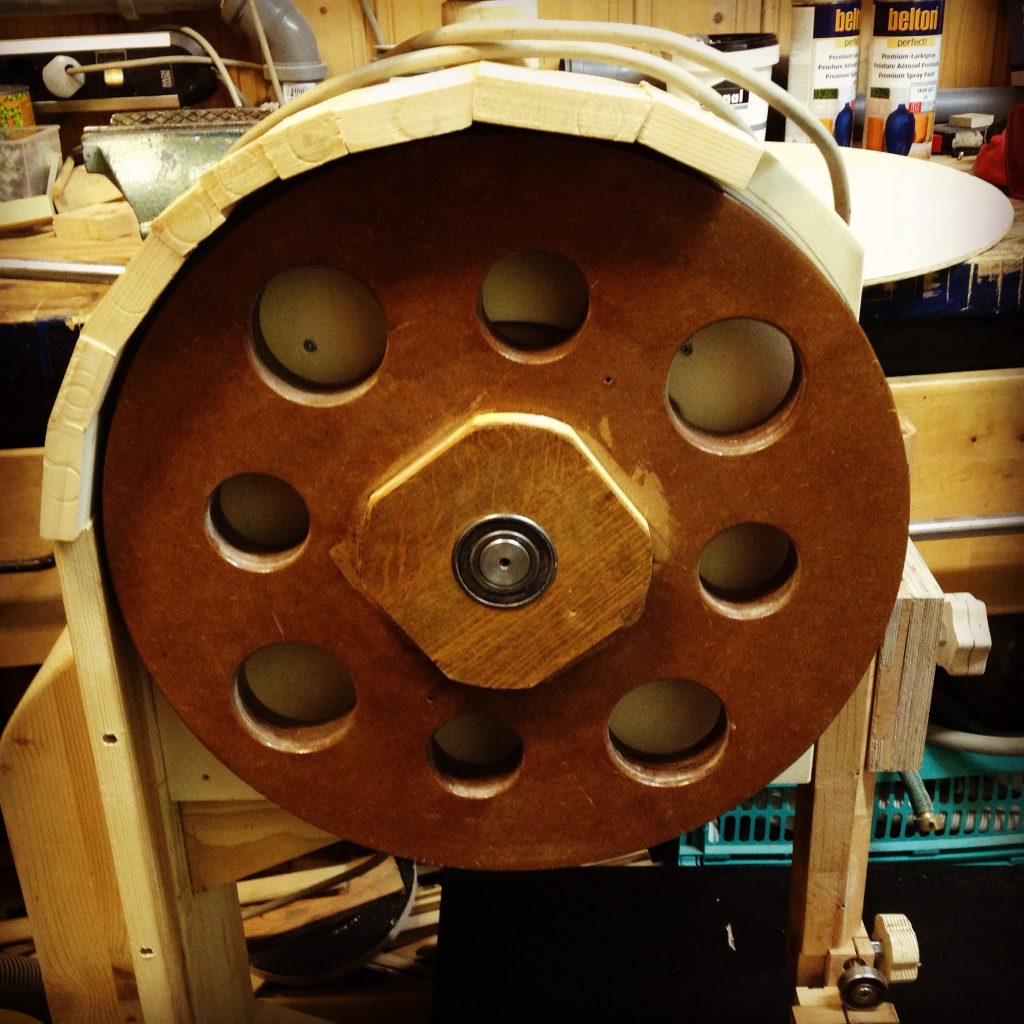
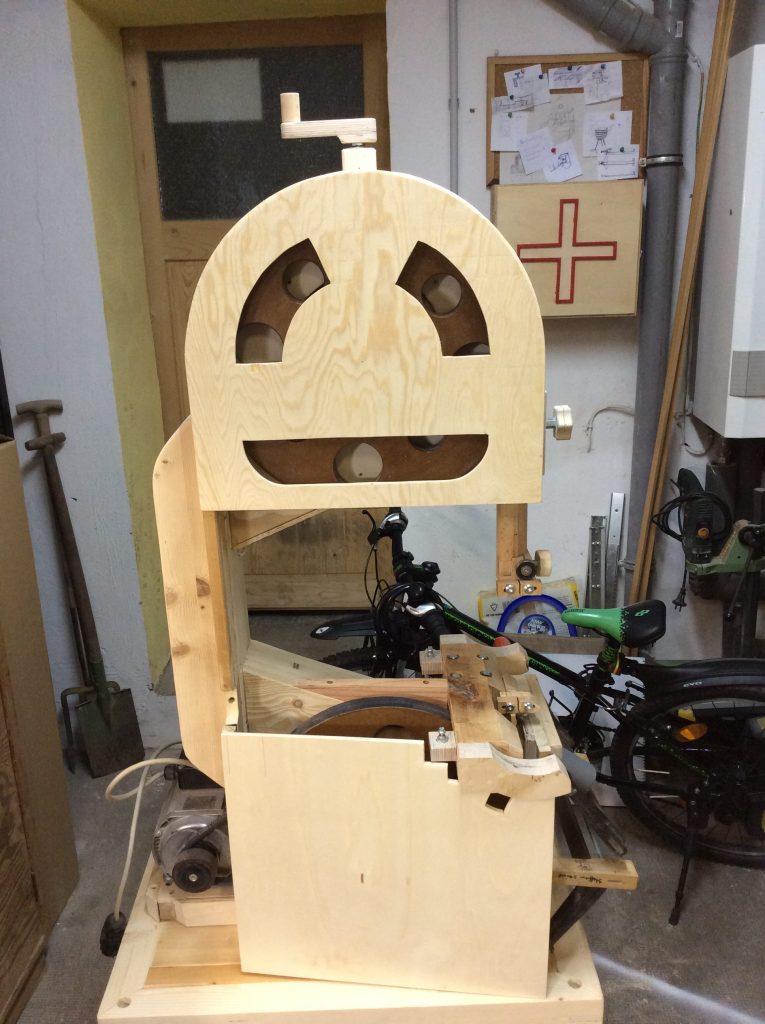
In die Aussparungen an der oberen Abdeckung wurden dann im Laufe der weiteren Arbeiten, noch 5 mm Plexiglasscheiben eingesetzt um den Rädern beim Drehen zuschauen zu können 😉
Oberflächenbehandlung der Einzelteile
Als nächster Schritt kam nun das Zwischenschleifen vor dem ersten Lackauftrag am Rahmen dran. Das konnte ich, dank des beim Triton Giveaway gewonnenen Exzenterschleifers und meines schon etwas betagten Deltaschleifers von Parkside relativ entspannt erledigen was auch nicht so viel Zeit in Anspruch nahm. Nun konnte ich endlich den Bootslack auf dem Rahmen aufbringen und nach benötigter Trocknungszeit von gut 24 Stunden das Ergebnis bewundern.
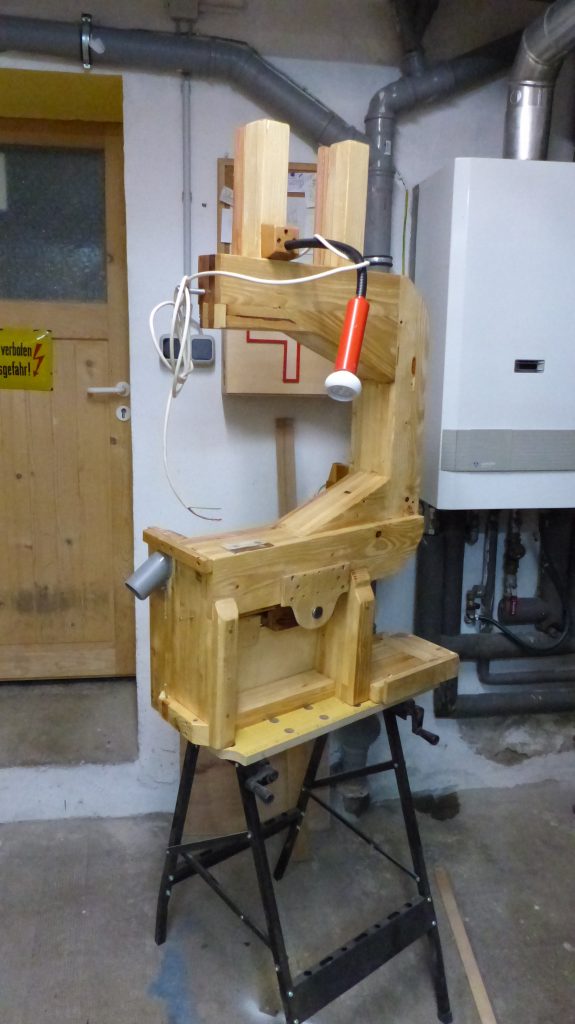
Wie im Bild zu sehen, waren dabei schon die meisten mit dem Rahmen verbundenen Teile schon angebaut. Jene Teile welche später moniert wurden, wie z.B. der komplette Sägetisch mit Halterung wurden extra behandelt. Die Abdeckungen welche der Sicherheit dienen, wurden vor der Lackierung noch mit farbiger Flüssigbeize behandelt und mehrfach geschliffen.
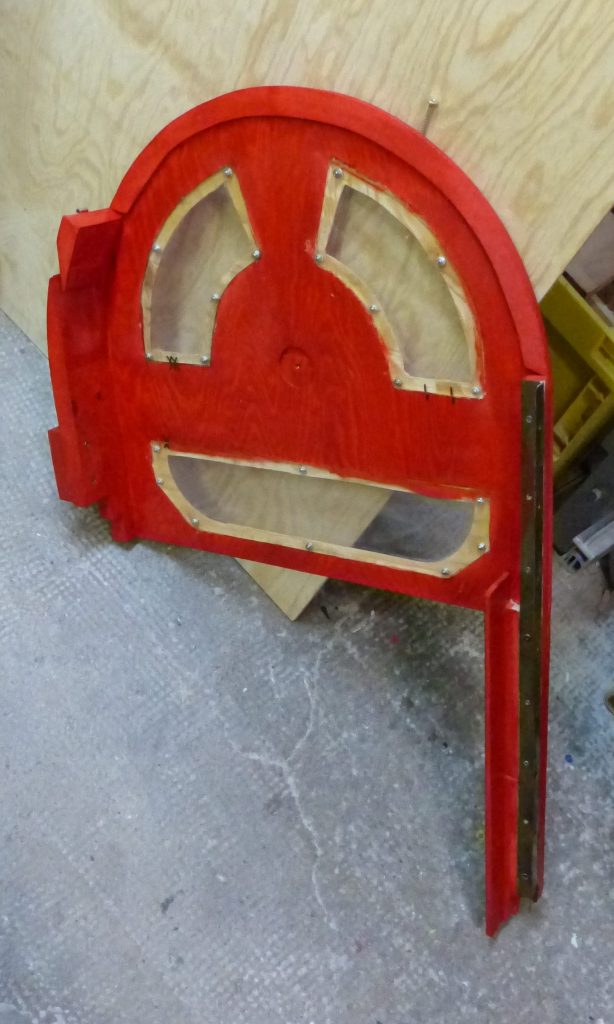
Alles in allem hat die Oberflächenbehandlung der Sägeteile, aufgrund der Trocknungszeiten von Beize und Lack fast eine Woche in Anspruch genommen. Dann kam endlich der Tag des Zusammenbaus und darauf hatte ich mich am meisten gefreut. Ich hatte zwar eine ungefähre Vorstellung wie meine Säge aussehen sollte, aber eine Vorstellung zu haben ist doch noch etwas anderes als eine fertige Säge vor sich stehen zu sehen.
Zusammenbau der Einzelteile zu einer Säge
Zunächst habe ich die untere und obere Radaufnahme am Rahmen befestigt und winklig ausgerichtet. Dann kam schon die untere Bandhalterung mit Trunion, was sich aber als leichter Fehler herausstellte. Ich hatte nun zwar die Radachsen schon montiert aber noch keine Räder drauf und mit installiertem Trunionhalter ging das untere Rad nicht auf die Achse zu schieben… Also, Trunionhalter wieder ab und Rad mit aufgelegtem Antriebsriemen einbauen. Nun konnte ich die komplette untere Halterung wieder anbringen und ausrichten. Nachdem anschließend das obere Rad an der Halterung montiert war kam, sehnsüchtig erwartet, das Sägeband drauf! Ein Testsägeschnitt war dann nur normal. Der Test war OK und ich konnte das Sägeband und die obere Halterung wieder abnehmen. Weiter ging der Zusammenbau mit der Montage der oberen und unteren Verkleidung der Räder und dem Einbau der Selben.

Nach dem Abschluss der Montage, folgte die Installation der elektrischen Einrichtungen wie der Steuerung für Beleuchtung und Antrieb und natürlich, ganz wichtig die Sicherheitseinrichtungen wie Türschalter und Notaus. Die folgenden Bilder sprechen für sich.
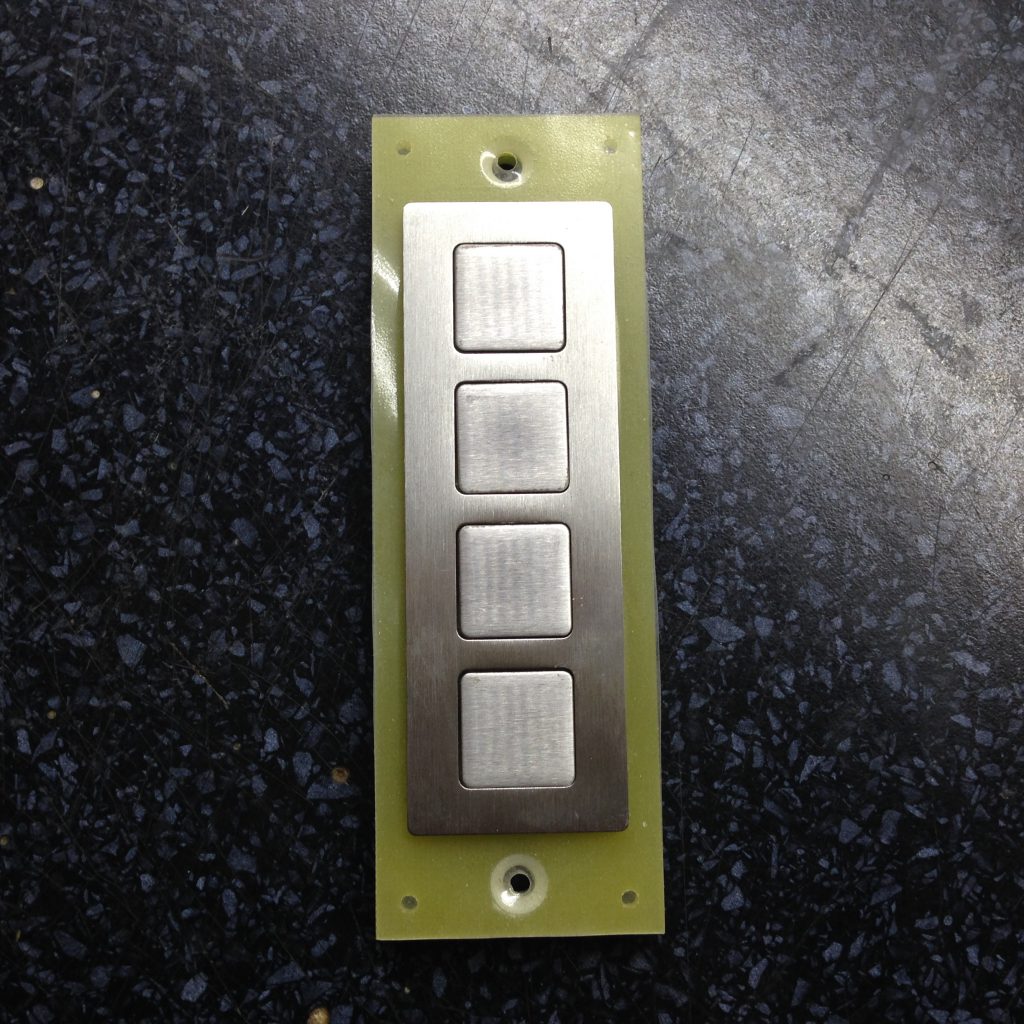
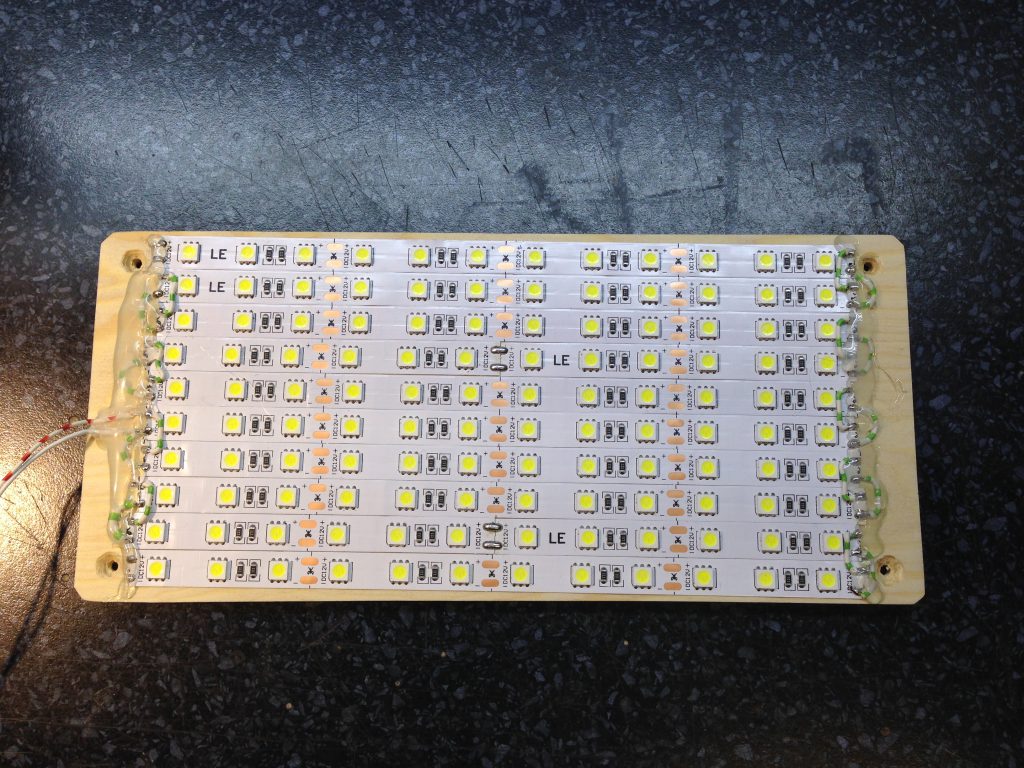
Die Flächenbeleuchtung aus LED-Stripes …
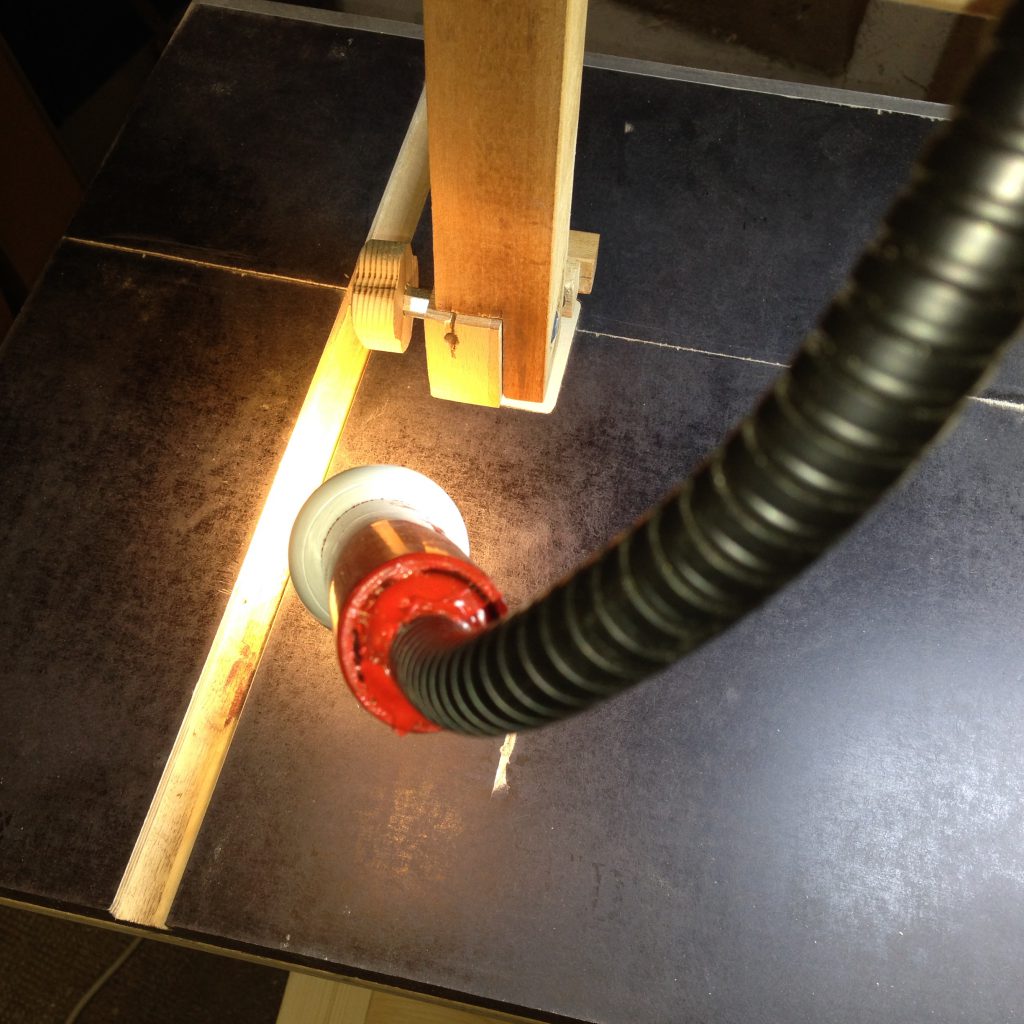
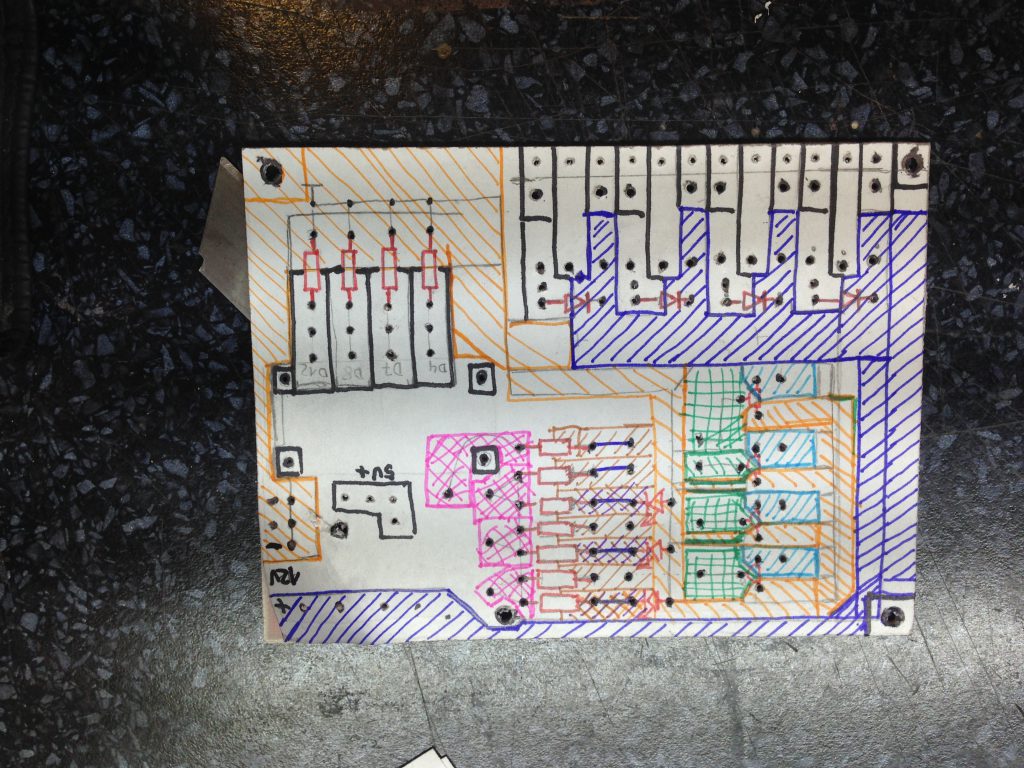
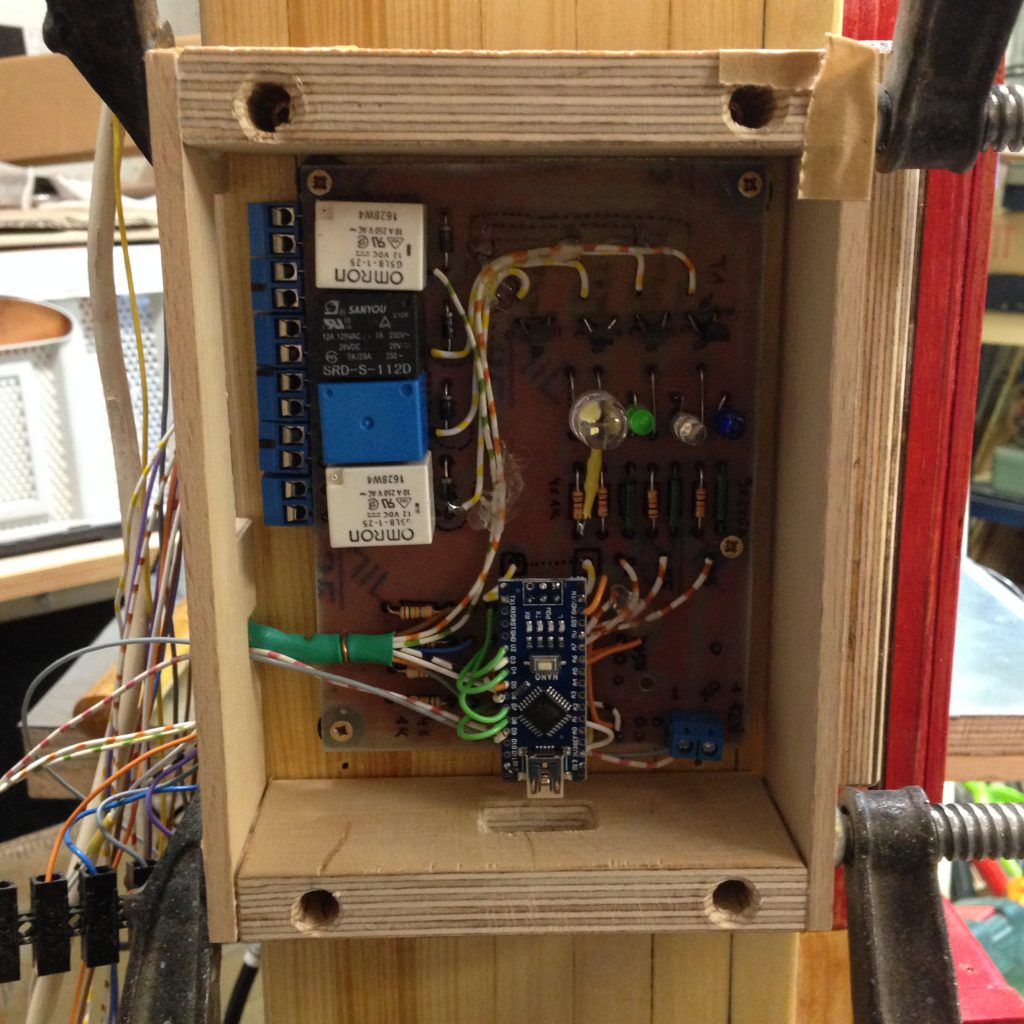
Gut zu sehen, der Arduino Nano.
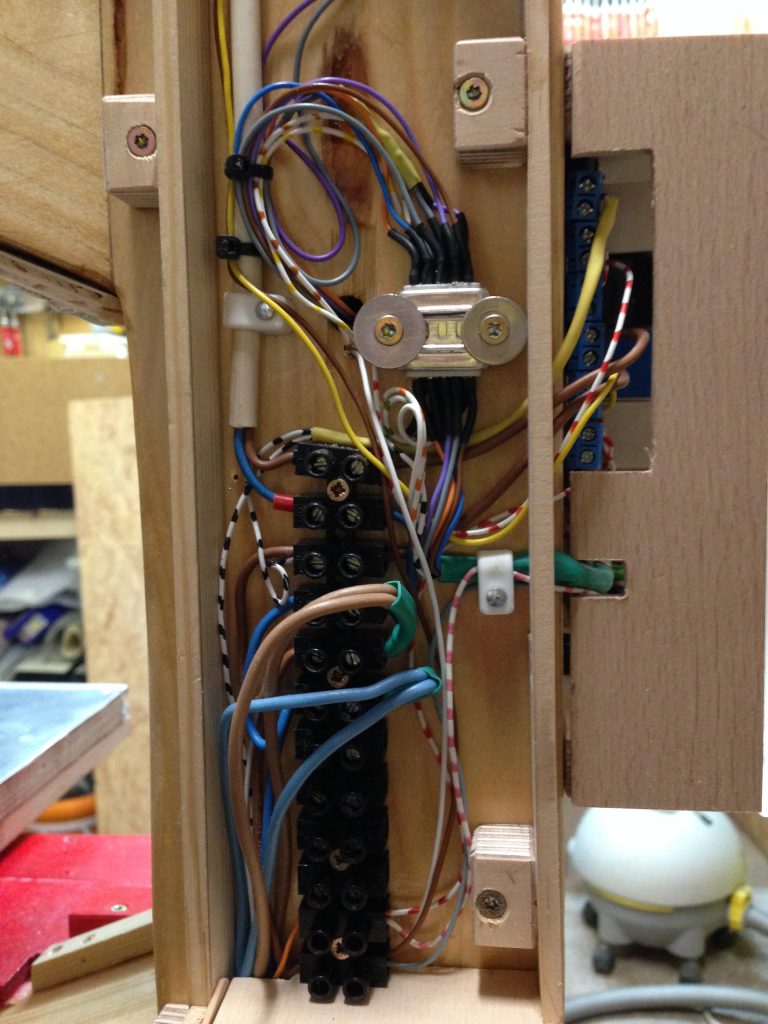
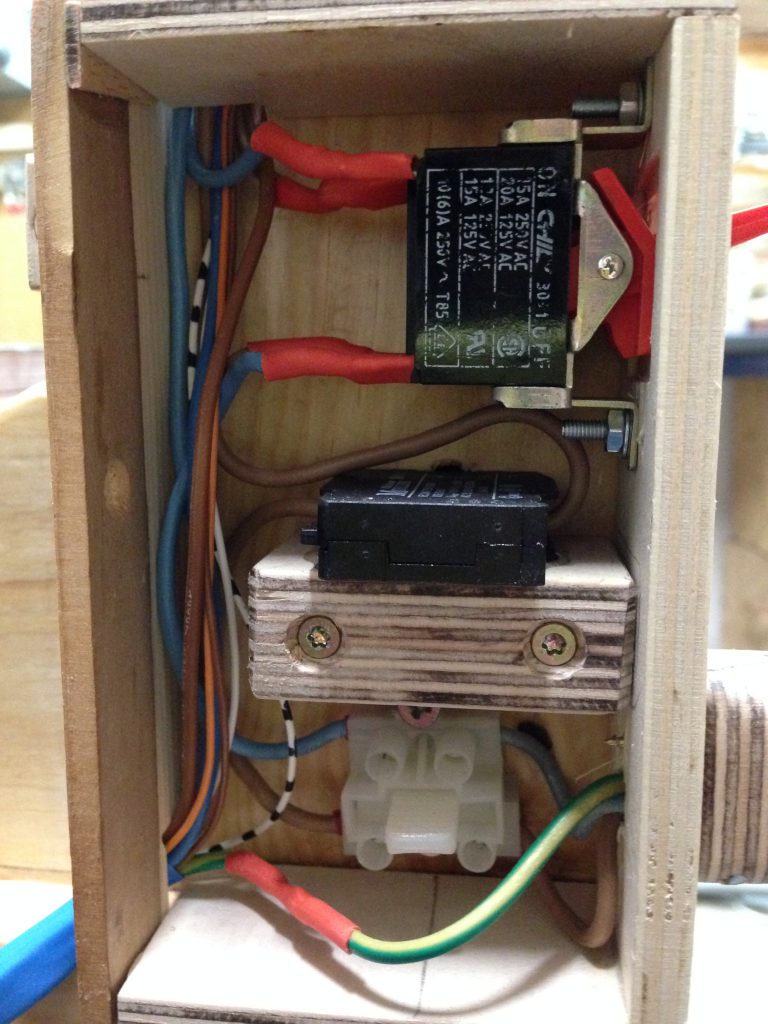
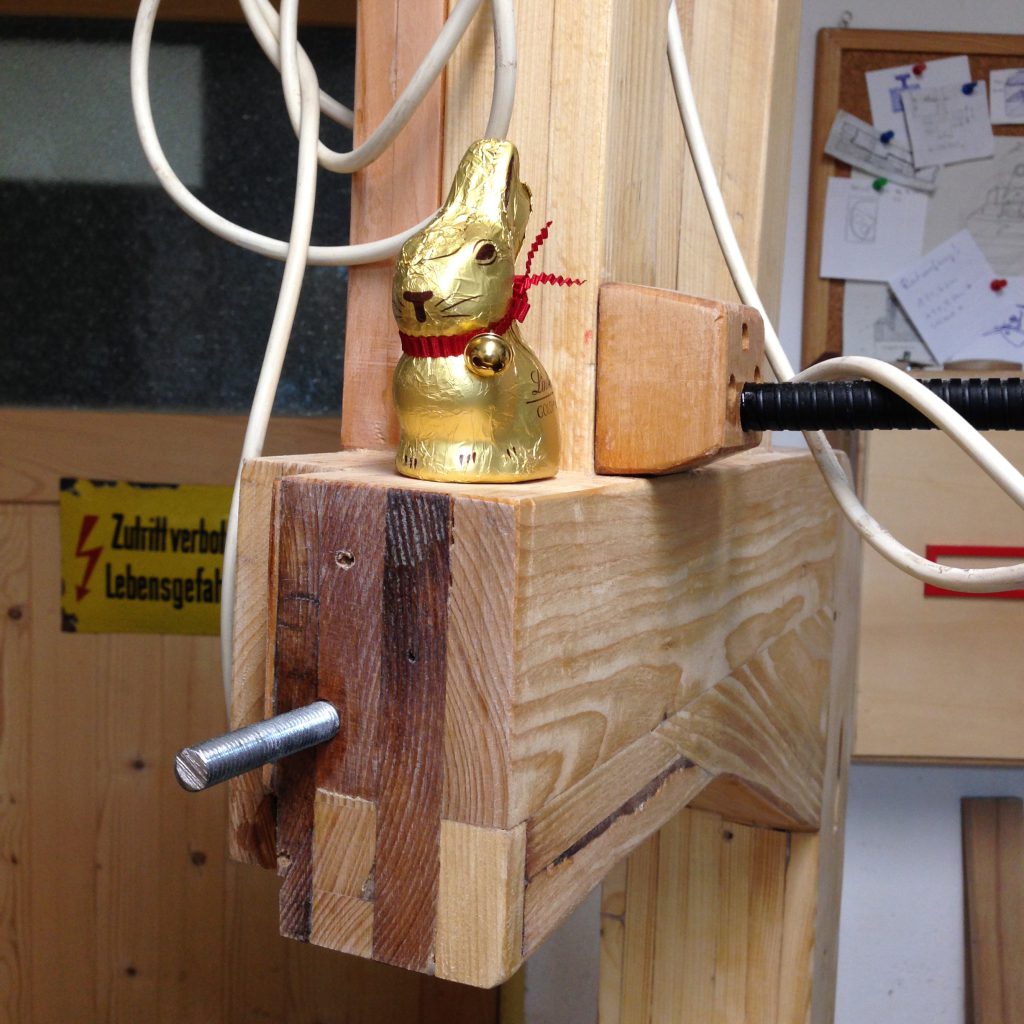
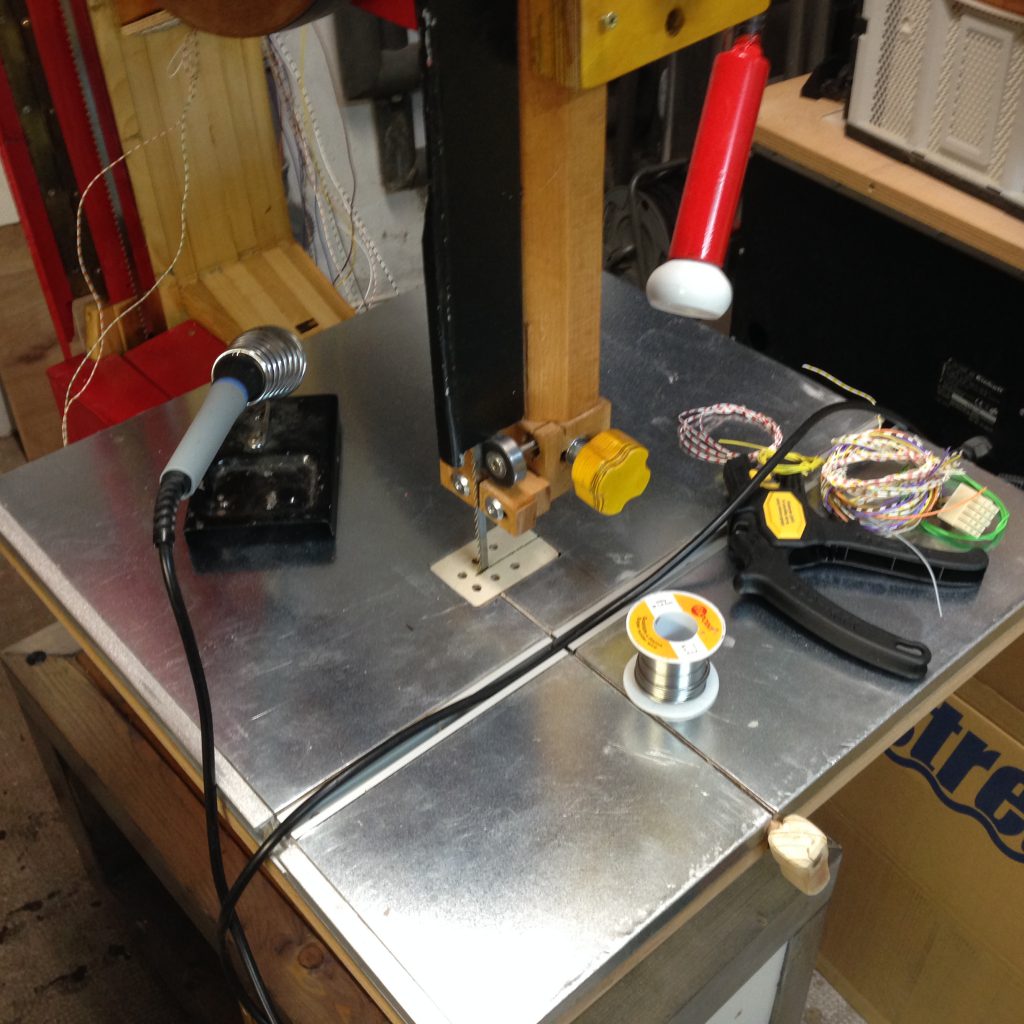
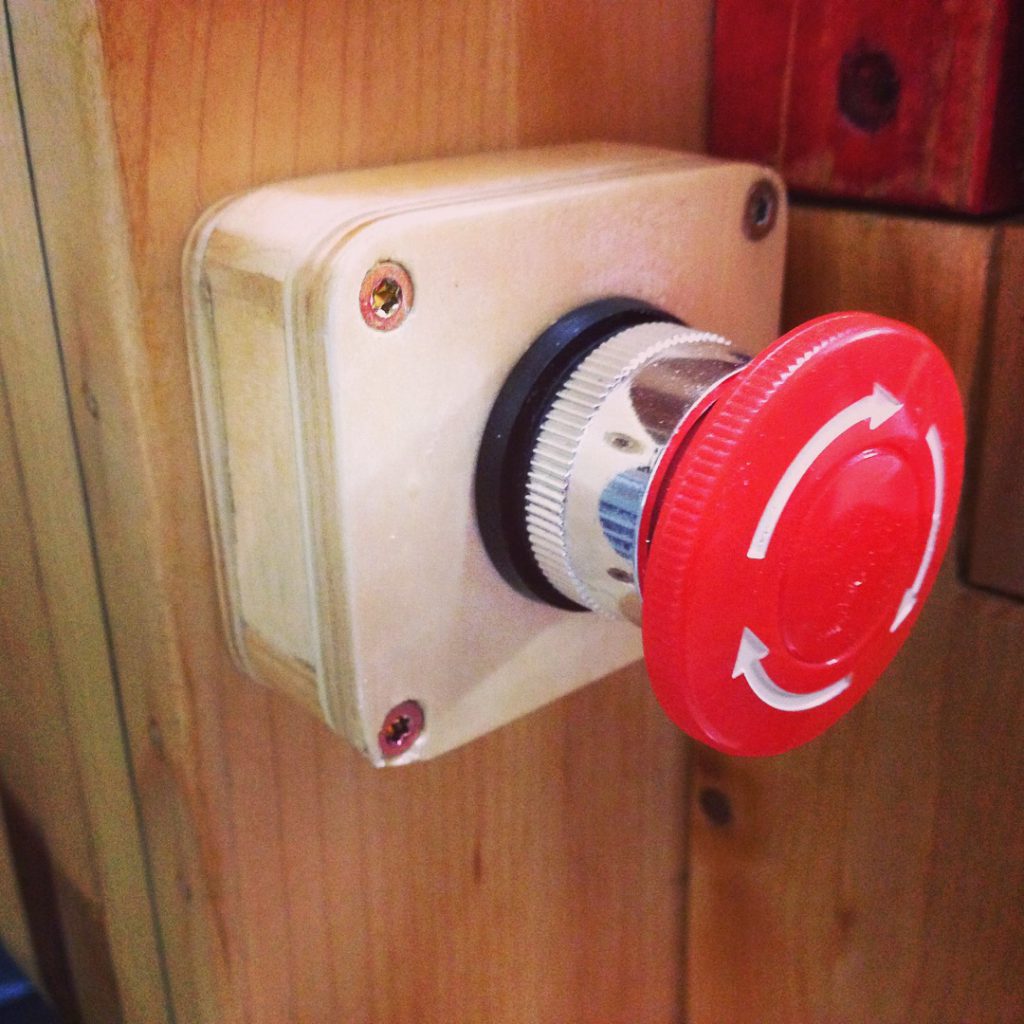
Über eine Druckstange die durch den Rahmen reicht, betätigt er den Notausschalter.
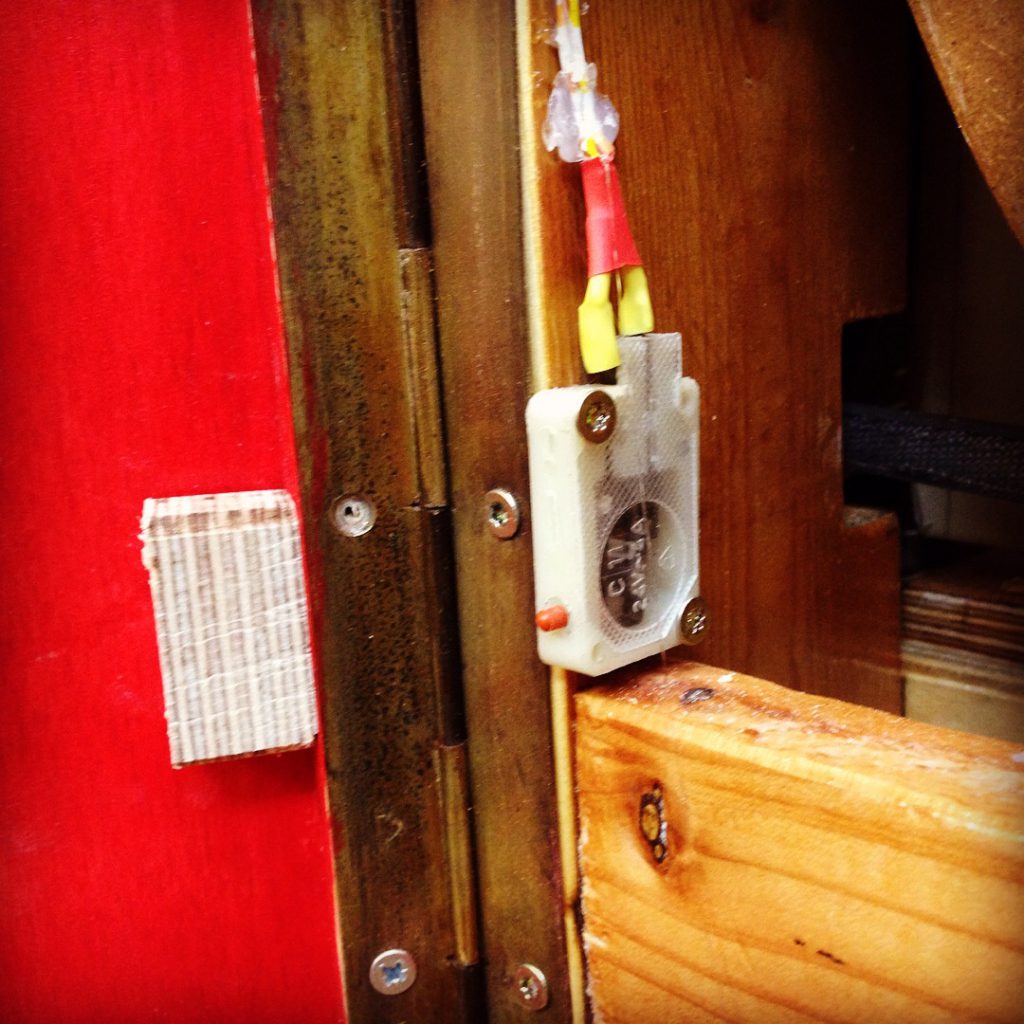
Auch an der oberen Tür gibt es einen solchen.
Nachdem die Elektrik eingebaut, angeschlossen und getestet war, konnte die „Endmontage“ und Vervollständigung der Bandsäge beginnen. Dazu zählte dann der weiter oben schon zu sehende Sägetisch mit Stahlbelag ein Paralellanschlag und die Absaugeinrichtung.
Der Sägetisch
Der Sägetisch wurde aus einer 22mm starken Siebdruckplatte gefertigt und mit T-Nut Schienen und auswechselbaren Sägebandausschnitten versehen. Um die Oberfläche haltbarer zu gestalten, haabe ich eine 0,5mm Stahlblechauflage angebacht. Diese kann einfach mit „Silbergleit“ behandelt werden und sorgt dann dafür, dass das Material leicht über den Sägetisch gleitet. Die obere T-Nut Schiene ist fürdie Führung von Sägeschlitten und dem Lochkreisschneider so wie ühnlichen Vorrichtungen in der Zukunft gedacht.
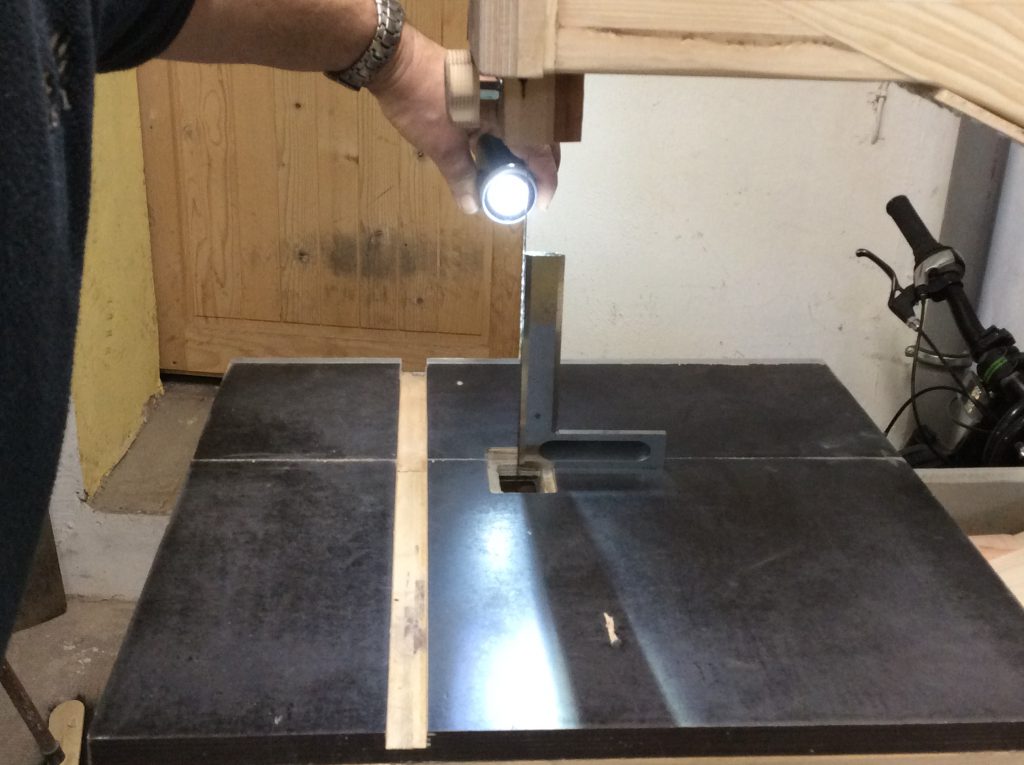
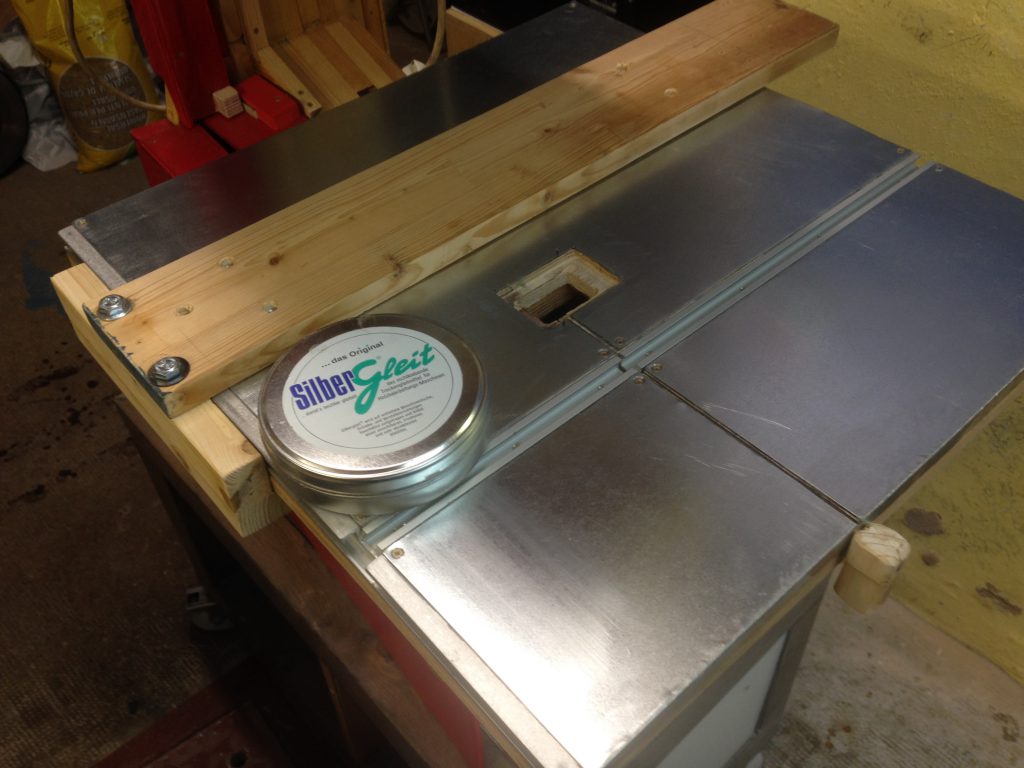
Und schon im Ansatz: der Parallelanschlag.
Der Parallelanschlag
Was ich unbedingt haben wollte, war ein stabiler Paralellanschlag um saubere und wiederholgenaue Schnitte und (durch auswechseln der Führungswange) auch Stämme auftrennen zu können. Zu diesem Zweck war in der Stirnseite des Sägetisches eine T-Nut Schiene eingelassen worden um den Anschlag zumindest vorne richtig festklemmen zu können. Als weiteres Feature, bekam der Anschlag eine hintere Klemmbacke, die über eine Gewindestange undd ein Stellrad angezogen werden kann.
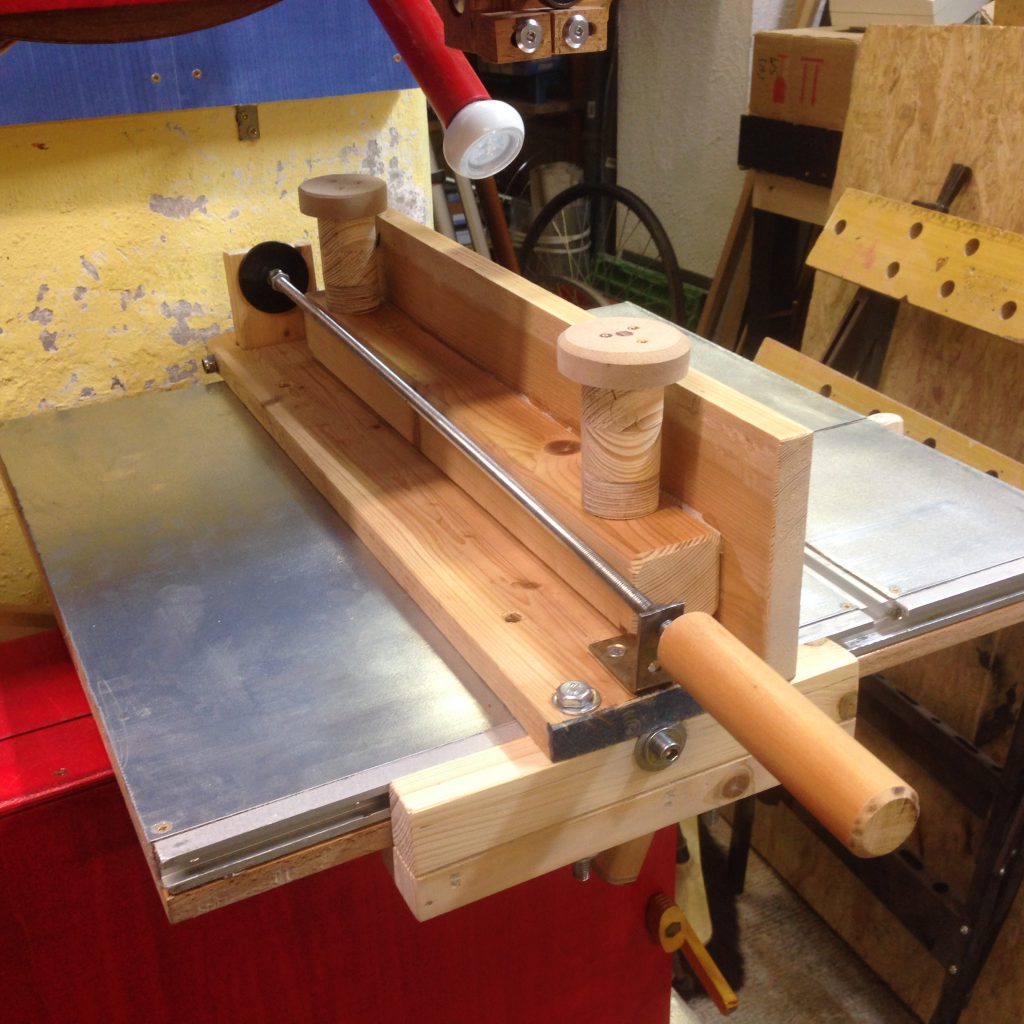
Ursprünglich war als Klemmbetätigumg oben zu sehender Griff angebracht, aber nach einiger Zeit der (umständlichen) Bedienung wurde dann ein Kurbelrad angebracht, was den Spannvorgang um einiges beschleunigte. Die Hauptfestigkeit kommt aber nach wie vor von der vorn angebrachten Inbus Schraube die einen „Spannstein“ in der T-Nut Schiene anzieht.
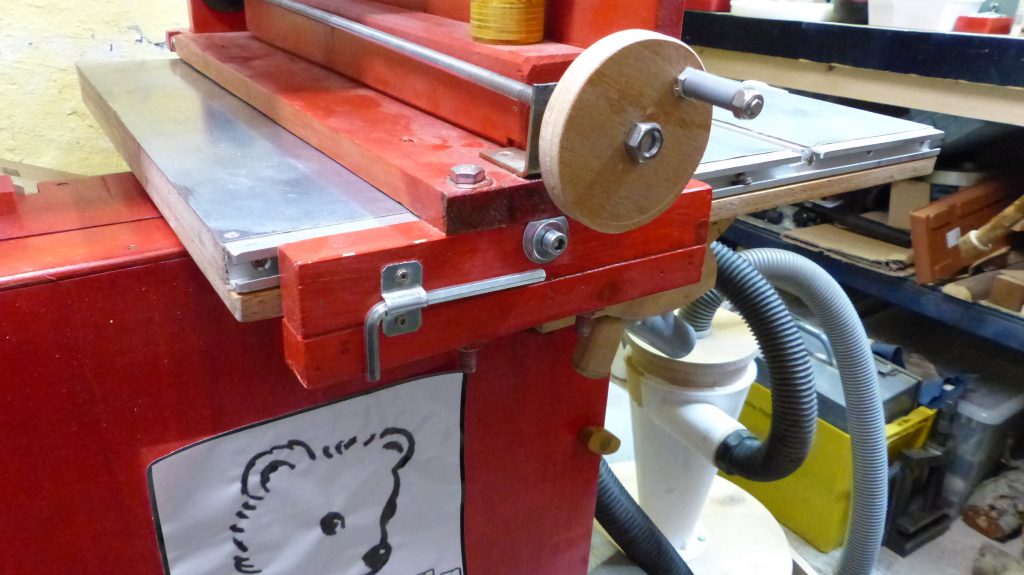
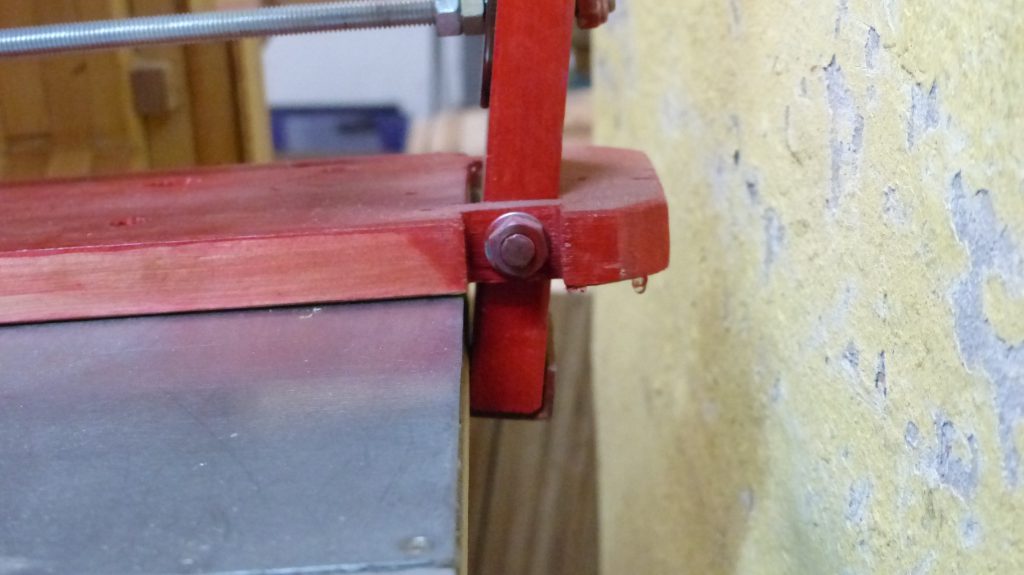
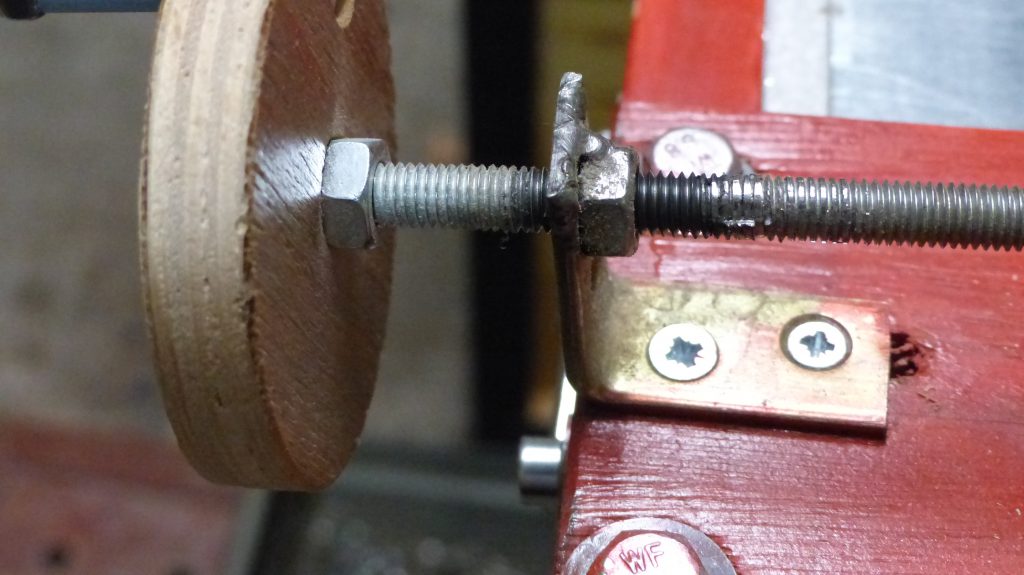
Schiebeschlitt(ch)en
Dieser kleine Schiebeschlitten ist sehr praktisch für das genaue Ablängen von Latten und Leisten. Er besitzt an der Unterseite eine Führungsleiste, die in der T-Nutschiene spielfrei läuft. Der Anschlag steht im Winkel von 90° zu Sägeband und oberer T-Nutschiene. Nachteil dieser Vorrichtung ist die begrenzte ablängbare Länge des Werkstücks.
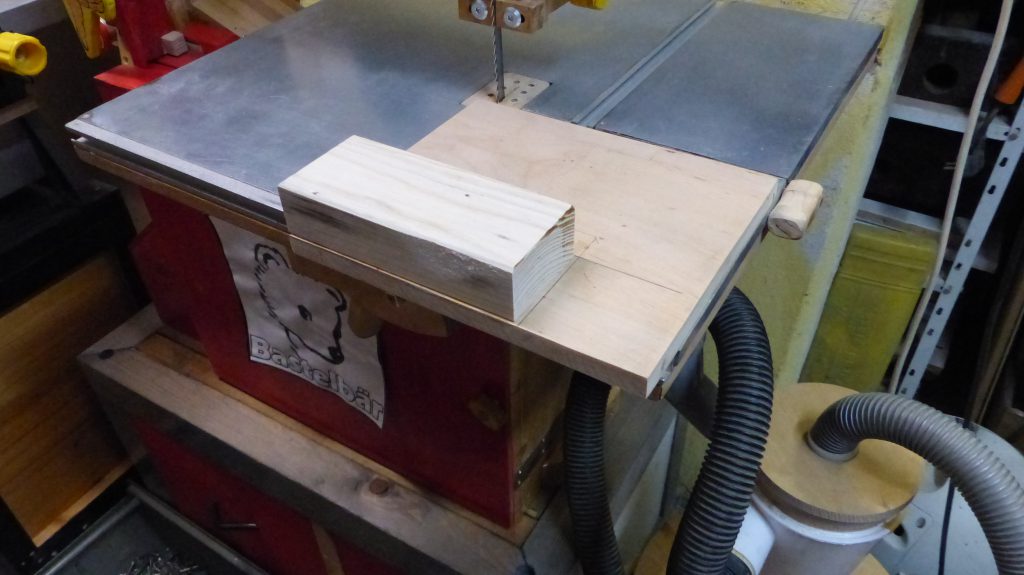
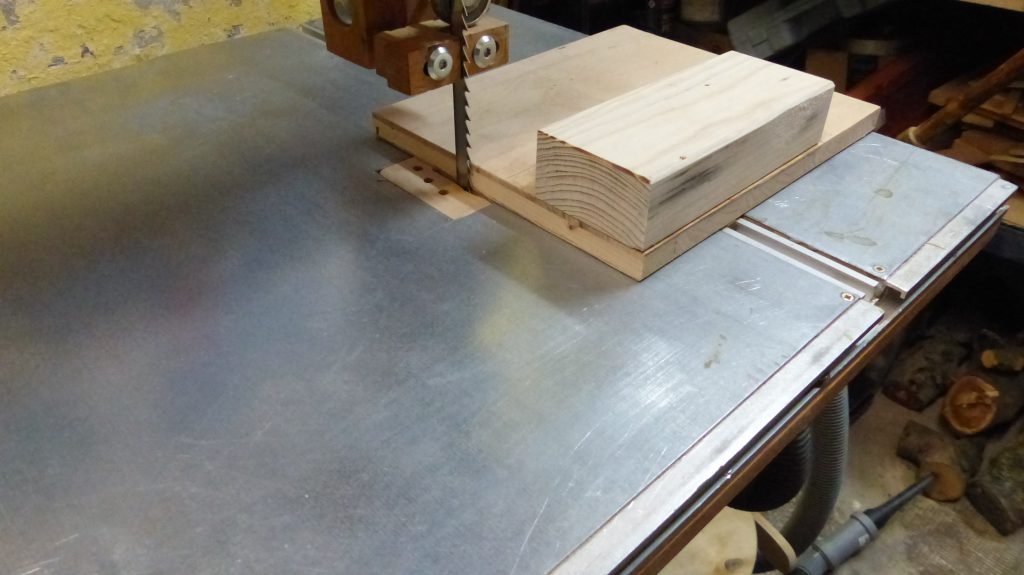
Kreisschneider
Der Kreisschneider wurde nach diesem Prinzip schon oft im Internet vorgestellt. Auch ich habe da nur die Anpassungen vorgenommen, die meine Bandsäge erfordert hat.
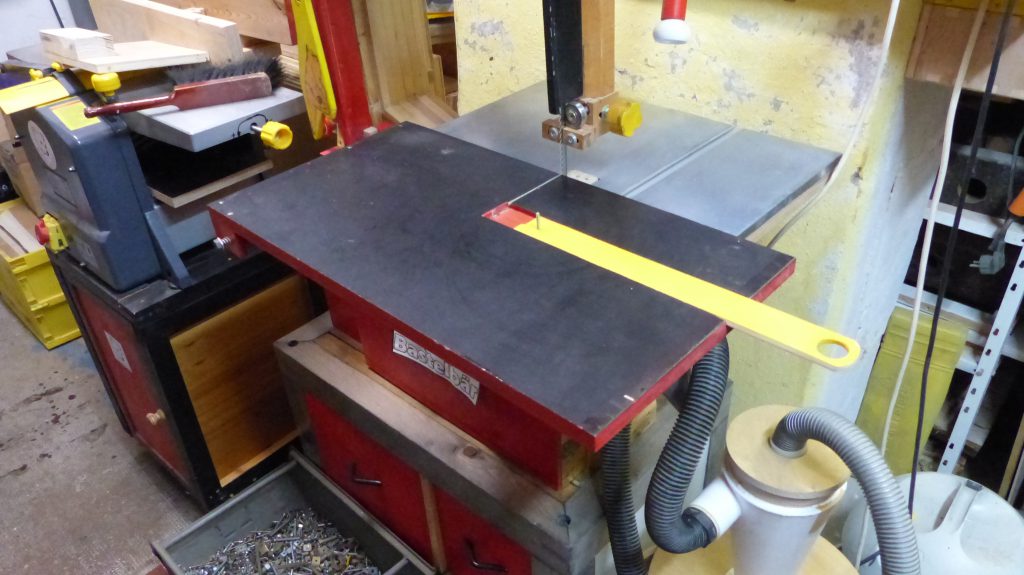
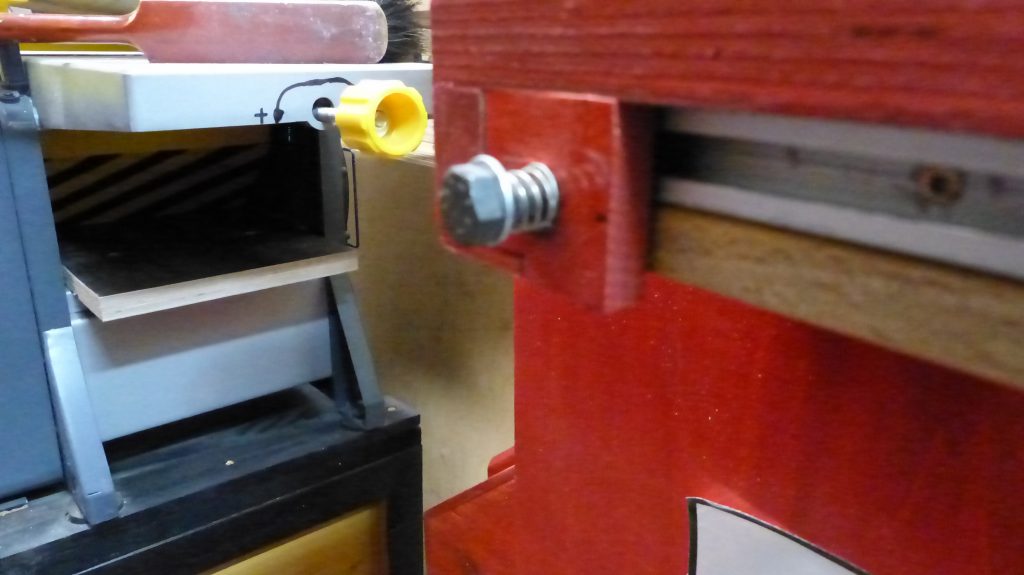
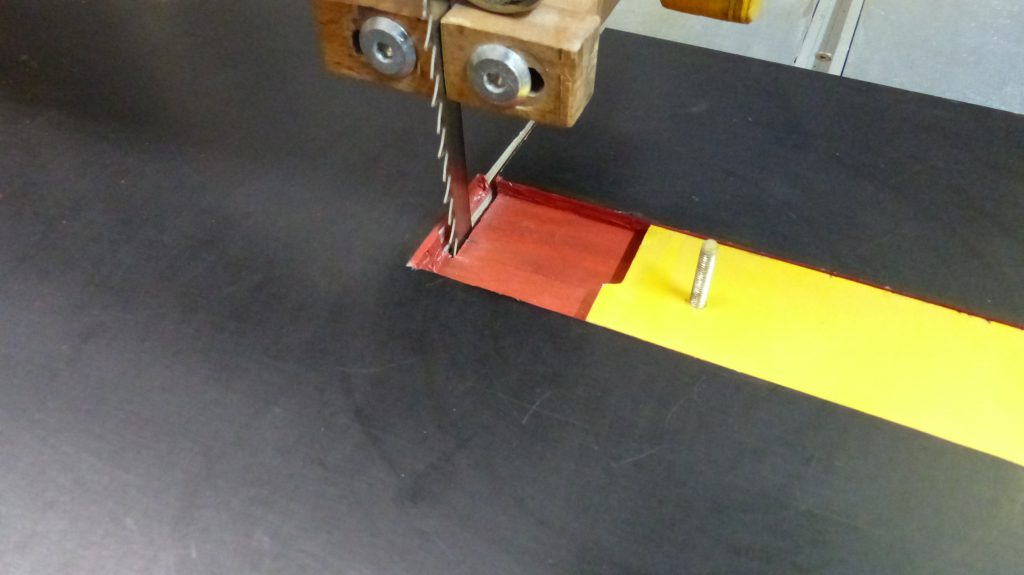